Reverse resolving mathematical algorithm for five shaft five ring parallel moving mechanism moving control
A motion control and mathematical algorithm technology, applied in the field of machinery, can solve problems such as the small size of the machine tool in the effective working space, the small deflection angle of the motion platform, and the inability to perform five-sided machining.
- Summary
- Abstract
- Description
- Claims
- Application Information
AI Technical Summary
Problems solved by technology
Method used
Image
Examples
Embodiment 1
[0059] Q 4 Coordinates, (-630.03, 363.75, 900); H 4 =75;
[0060] Q 5 Coordinates, (-472.98, -273.07, 1444.92); H 5 = 250;
[0061] by Q i Point coordinates can be obtained B i =(B cos β i , B sin β i ,0) T coordinate of
[0062] B 1 =(B x1 , B y1 ,0)=(472.98,-273.07,0)
[0063] B 2 =(B x2 , B y2 0) = (630.03, 363.75, 0)
[0064] B 3 =(B x3 , B y3 0) = (0, 510.09, 0)
[0065] B 4 =(B x4 , B y4 0) = (-630.03, 363.75, 0) L iThe general term formula is a parametric formula, that is, as long as it is a five-axis five-ring parallel mechanism, the structural size of the mechanism can be changed arbitrarily. The structural dimensions include the radius A of the moving platform, and the Q of the fixed frame of the rods i dot, Q i =(B cos β i , B sin β i ,q i ) T ;The distance H between each ring and the x′-y′ plane of the moving coordinate system i .
[0066] Through the modeling of the mechanical three-dimensional design software SolidWorks, a virt...
PUM
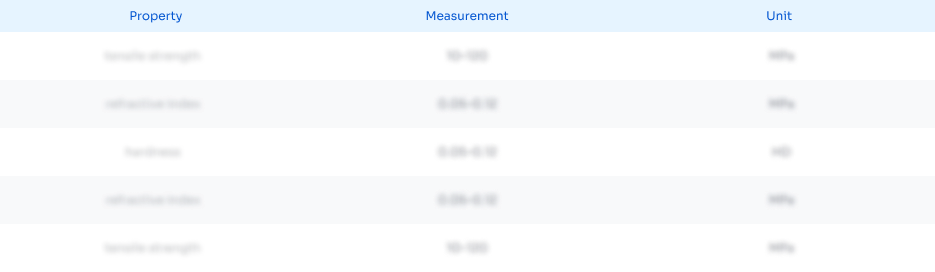
Abstract
Description
Claims
Application Information

- R&D Engineer
- R&D Manager
- IP Professional
- Industry Leading Data Capabilities
- Powerful AI technology
- Patent DNA Extraction
Browse by: Latest US Patents, China's latest patents, Technical Efficacy Thesaurus, Application Domain, Technology Topic, Popular Technical Reports.
© 2024 PatSnap. All rights reserved.Legal|Privacy policy|Modern Slavery Act Transparency Statement|Sitemap|About US| Contact US: help@patsnap.com