Projecting structural optical space position and shape multi-point fitting calibrating method
A space position, fitting calibration technology, applied in the direction of using optical devices, measuring devices, instruments, etc., can solve the problems of difficulty in controlling accuracy and consistency, deformation of projected structured light, and difficulty in improving accuracy, achieving easy on-site calibration, reducing The effect of increased complexity, precision
- Summary
- Abstract
- Description
- Claims
- Application Information
AI Technical Summary
Problems solved by technology
Method used
Image
Examples
Embodiment Construction
[0012] In order to better understand the technical solution of the present invention, a further detailed description will be given below in conjunction with the accompanying drawings and embodiments.
[0013] Such as figure 1 As shown, it is a schematic diagram of the multi-point fitting calibration method for the spatial position and shape of projected structured light according to the present invention. With the center of the lens of the two-dimensional imaging device as the origin and its optical axis as the OZ axis, the coordinate system OXYZ of the two-dimensional imaging device is established. The two-dimensional imaging device adopts any existing two-dimensional imaging technology, such as CCD camera, CMOS General imaging devices such as cameras, PSD position sensitive sensors, etc. The projection method of the projection device can adopt any existing two-dimensional projection structured light technology, such as line laser projection, grating projection, color struct...
PUM
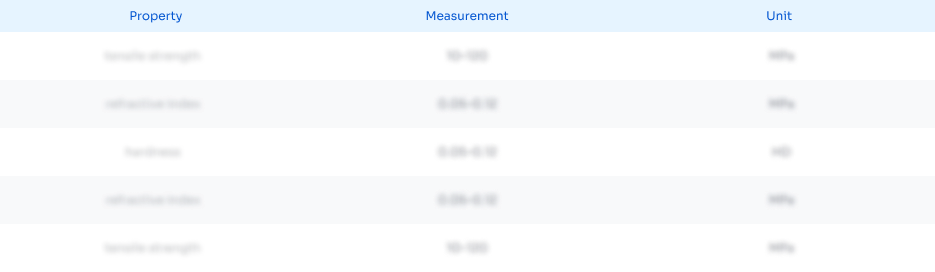
Abstract
Description
Claims
Application Information

- R&D
- Intellectual Property
- Life Sciences
- Materials
- Tech Scout
- Unparalleled Data Quality
- Higher Quality Content
- 60% Fewer Hallucinations
Browse by: Latest US Patents, China's latest patents, Technical Efficacy Thesaurus, Application Domain, Technology Topic, Popular Technical Reports.
© 2025 PatSnap. All rights reserved.Legal|Privacy policy|Modern Slavery Act Transparency Statement|Sitemap|About US| Contact US: help@patsnap.com