Aluminium alloy foil for founding and rolling automotive heat radiator fin billet and manufacturing method thereof
A technology for automobile radiators and aluminum alloy foils, which is applied in the manufacture of aluminum alloy foils and the field of aluminum alloy foils for heat exchanger fins, and can solve problems such as not being able to fully meet the specific requirements of foils for automobile radiator fins
- Summary
- Abstract
- Description
- Claims
- Application Information
AI Technical Summary
Problems solved by technology
Method used
Examples
Embodiment 6
[0039] Embodiment 6: the chemical composition ratio of material is:
[0040] Component
iron
copper
aluminum
Weight ratio
0.55
0.50
0.04
1.0
1.8
0.015
the remaining
[0041] The manufacturing method of aluminum alloy foil for radiator fins is as follows:
[0042] 1) Casting and rolling of slab:
[0043] Casting area length mm
Front box temperature ℃
Casting speed mm / min
Water pressure MPa
60
690
1000
30
0.6
[0044] 2) Cold rolling of strip:
[0045] The cast-rolled slab is rolled through 8 passes to a predetermined thickness, and the cold working rate from this thickness to the finished product thickness is controlled to 50%. Intermediate annealing is performed at this thickness, the annealing temperature is 380°C, and the holding time is 18 hours. Then go through 1 pa...
PUM
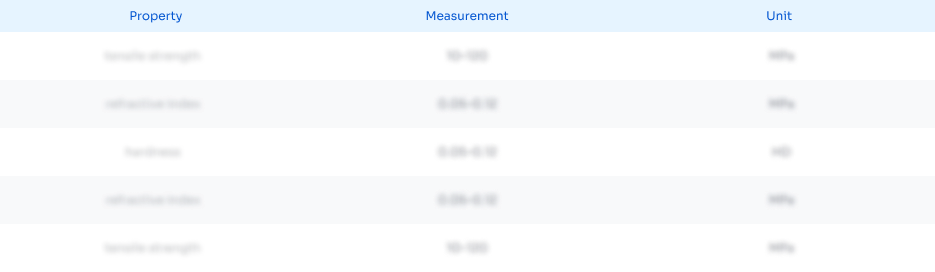
Abstract
Description
Claims
Application Information

- R&D
- Intellectual Property
- Life Sciences
- Materials
- Tech Scout
- Unparalleled Data Quality
- Higher Quality Content
- 60% Fewer Hallucinations
Browse by: Latest US Patents, China's latest patents, Technical Efficacy Thesaurus, Application Domain, Technology Topic, Popular Technical Reports.
© 2025 PatSnap. All rights reserved.Legal|Privacy policy|Modern Slavery Act Transparency Statement|Sitemap|About US| Contact US: help@patsnap.com