Alignment detection structure and alignment offset detection method
A technology for detecting structures and detection methods, which is applied in the direction of machine/structural component testing, measuring electricity, and measuring devices, and can solve problems such as complex detection methods, roughly estimated offsets, and misalignment offsets
- Summary
- Abstract
- Description
- Claims
- Application Information
AI Technical Summary
Problems solved by technology
Method used
Image
Examples
Embodiment Construction
[0027] Please refer to the following figure 2 The alignment detection structure of a preferred embodiment of the present invention is described, which includes: a substrate 3 ; a color filter 4 ; and an alignment pattern 14 disposed in the die bonding area 5 on the substrate 3 . Since the following embodiments are described with the COG process, the substrate 3 is a glass substrate, but it should be noted that the present invention can also be applied to other lamination processes, such as plastic substrates.
[0028] image 3 It is an enlarged view of the alignment detection structure of the present invention, wherein the alignment pattern 14 is completely complementary to the alignment mark 15 on the chip. In addition, the alignment pattern 14 has a first frame 16 with a known first width 17 located around the alignment pattern 14 . In this embodiment, the alignment marks 15 on the chip are cross-shaped, and the alignment patterns 14 are four square patterns located at fo...
PUM
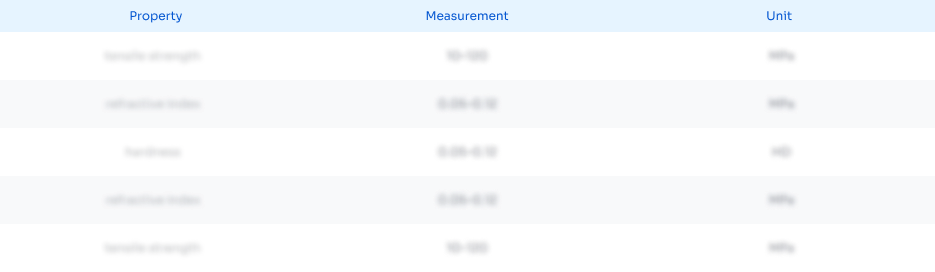
Abstract
Description
Claims
Application Information

- R&D
- Intellectual Property
- Life Sciences
- Materials
- Tech Scout
- Unparalleled Data Quality
- Higher Quality Content
- 60% Fewer Hallucinations
Browse by: Latest US Patents, China's latest patents, Technical Efficacy Thesaurus, Application Domain, Technology Topic, Popular Technical Reports.
© 2025 PatSnap. All rights reserved.Legal|Privacy policy|Modern Slavery Act Transparency Statement|Sitemap|About US| Contact US: help@patsnap.com