Manufacturing method of high purity calcium carbonate for electron industry
A technology of electronic industry and manufacturing method, which is applied in the field of manufacturing high-purity calcium carbonate for electronic industry, can solve the problems of complex process and high cost, and achieve the effect of high purity and low heavy metal impurities
- Summary
- Abstract
- Description
- Claims
- Application Information
AI Technical Summary
Problems solved by technology
Method used
Image
Examples
Embodiment 1
[0059] Calcium nitrate Ca(NO 3 ) 2 and sodium carbonate Na 2 CO 3 As raw material, Ca(NO 3 ) 2 Remove impurities and decolorize twice at pH10 and pH12; Na 2 CO 3 Remove impurities and decolorize once at pH 12; synthetic reaction of two raw materials, temperature 40--45°C, 35 minutes, after standing for 20 minutes, stir for 5 minutes, centrifuge and dehydrate, wash with purified water at 50°C±10°C until there is no chloride ion , 130-140 ℃ drying to get the finished product.
Embodiment 2
[0061] Calcium Chloride CaCl 2 and sodium carbonate Na 2 CO 3 As raw material, CaCl 2 At pH9, pH12, and pH14, precipitate for three times to remove impurities and decolorize; Na 2 CO 3 Precipitate at pH 14 to remove impurities and decolorize once; synthesis reaction of two raw materials, temperature 25--35°C, 30 minutes, stirring for 25 minutes, after centrifugation and dehydration, wash with purified water at 70±10°C until there is no chloride ion, 130--140°C Dried to get the finished product.
Embodiment 3
[0063] Calcium Chloride CaCl 2 with ammonium bicarbonate NH 4 HCO 3 For the raw material. CaCl 2 Add hydrogen peroxide at pH 6; pH 9, pH 12, and pH 14 for three precipitations to remove impurities and decolorize; add thioacetamide at pH 10 to remove heavy metal impurities. NH 4 HCO 3 At pH9, pH12 twice to remove impurities and decolorize. The two solutions were reacted at 35-040°C for 25 minutes, left to stand for 20 minutes, stirred for 5 minutes, the resultant was washed with warm water at 50±10°C until free of chloride ions, and dried at 120-130°C to obtain the finished product.
[0064] serial number
PUM
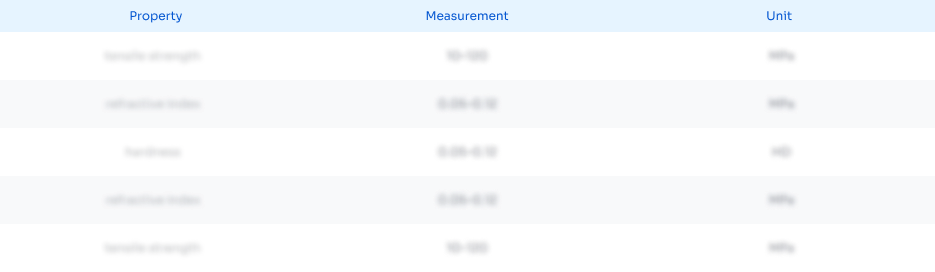
Abstract
Description
Claims
Application Information

- R&D Engineer
- R&D Manager
- IP Professional
- Industry Leading Data Capabilities
- Powerful AI technology
- Patent DNA Extraction
Browse by: Latest US Patents, China's latest patents, Technical Efficacy Thesaurus, Application Domain, Technology Topic, Popular Technical Reports.
© 2024 PatSnap. All rights reserved.Legal|Privacy policy|Modern Slavery Act Transparency Statement|Sitemap|About US| Contact US: help@patsnap.com