Wood rapid-drying method
A wood drying and fast drying technology, applied in drying solid materials, heating to dry solid materials, drying, etc., can solve the problems of slow drying speed, increased energy consumption, large power consumption, etc., to speed up drying speed and save energy energy effect
- Summary
- Abstract
- Description
- Claims
- Application Information
AI Technical Summary
Problems solved by technology
Method used
Examples
Embodiment 1
[0021] Example 1: Put 50mm thick oak wood (with a density of about 0.7 g / cm 3 ) Is placed in a wood drying chamber, the ratio of the cross-sectional area of the inlet and exhaust ducts in the wood drying chamber to the total volume of the chamber is 0.01. Close the intake and exhaust ducts of the wood drying room, turn on the fan and heater in the wood drying room, and at the same time spray steam into the wood drying room at a pressure of 0.5 MPa through the steam jet pipe to make the steam in the wood drying room reach a saturated state . Raise the wood drying chamber from 30°C to 80°C within 9-10 hours, maintain the temperature of the wood drying chamber at 80°C and keep it warm for 7 hours, then turn off the heater of the wood drying chamber and open the inlet and exhaust ducts , Within 4 hours, the temperature of the wood drying chamber is rapidly reduced by 40℃~48℃, and then the intake and exhaust ducts are closed. Immediately afterwards, repeat the above rapid heating, he...
Embodiment 2
[0022] Example 2: The 30mm thick Catalpa wood (with a density of about 0.5 g / cm 3 ) Is placed in a wood drying chamber, the ratio of the cross-sectional area of the inlet and exhaust ducts in the wood drying chamber to the total volume of the chamber is 0.01. Close the intake and exhaust ducts of the wood drying room, turn on the fan and heater in the wood drying room, and at the same time spray steam into the wood drying room at a pressure of 0.5 MPa through the steam jet pipe to make the steam in the wood drying room reach a saturated state . Make the wood drying chamber rise from 30°C to 90°C within 4 to 5 hours, keep the wood drying chamber at a temperature of 90°C and keep it warm for 4 hours, then turn off the heater of the wood drying chamber and open the inlet and exhaust ducts , In 2.5 hours, the temperature of the wood drying chamber is rapidly reduced by 30°C to 40°C, and then the inlet and exhaust ducts are closed. Immediately afterwards, the above-mentioned rapid he...
Embodiment 3
[0023] Example three: the 70mm thick pine wood (with a density of about 0.3 g / cm 3 ) Is placed in a wood drying chamber, the ratio of the cross-sectional area of the inlet and exhaust ducts in the wood drying chamber to the total volume of the chamber is 0.01. Close the intake and exhaust ducts of the wood drying room, turn on the fan and heater in the wood drying room, and at the same time spray steam into the wood drying room at a pressure of 0.5 MPa through the steam jet pipe to make the steam in the wood drying room reach a saturated state . Raise the wood drying chamber from 30°C to 95°C in 9-10 hours, maintain the temperature of the wood drying chamber at 95°C and keep it warm for 8 hours, then turn off the heater of the wood drying chamber and open the inlet and exhaust ducts , In 5 hours, the temperature of the wood drying chamber is rapidly reduced by 47℃~56℃, and then the intake and exhaust ducts are closed. Immediately afterwards, the above-mentioned rapid heating, he...
PUM
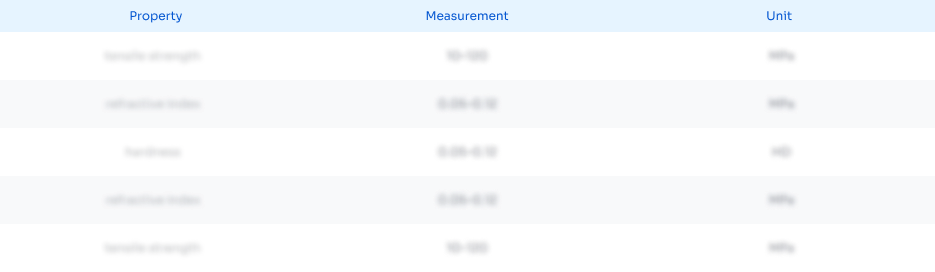
Abstract
Description
Claims
Application Information

- R&D Engineer
- R&D Manager
- IP Professional
- Industry Leading Data Capabilities
- Powerful AI technology
- Patent DNA Extraction
Browse by: Latest US Patents, China's latest patents, Technical Efficacy Thesaurus, Application Domain, Technology Topic, Popular Technical Reports.
© 2024 PatSnap. All rights reserved.Legal|Privacy policy|Modern Slavery Act Transparency Statement|Sitemap|About US| Contact US: help@patsnap.com