Welded golf club head
A golf club head and club head technology, applied to golf balls, golf clubs, rackets, etc., can solve time-consuming surface processing steps, complex structure of the ball hitting panel and club head body, unfavorable manufacturing and rapid pre-assembly, etc. problem, achieve the effect of increasing welding quality and avoiding incomplete welding
- Summary
- Abstract
- Description
- Claims
- Application Information
AI Technical Summary
Problems solved by technology
Method used
Image
Examples
Embodiment Construction
[0032] Such as figure 1 , figure 2 As shown, the present invention includes a club head body 1 and a ball head assembly that is a ball striking panel 2 .
[0033] The club head body 1 is a basic structure selected from existing golf club heads such as iron type, wood type or pusher type. The present invention is an example of an iron type golf club head, but other club head types can also be applied. same concept.
[0034] Such as figure 1 , figure 2 As shown, the club head body 1 is made from materials such as stainless steel, carbon steel, hemp aging steel, tungsten alloy, nickel-based alloy, titanium alloy, etc., and the club head body 1 is further set at an appropriate position, such as the position on the front of the ball. There is an assembly opening 11 , and the assembly opening 11 forms an inner peripheral welding surface 12 , a supporting bottom edge 13 and a diameter-reducing portion 14 in sequence toward the inside of the club head body 1 .
[0035] The inne...
PUM
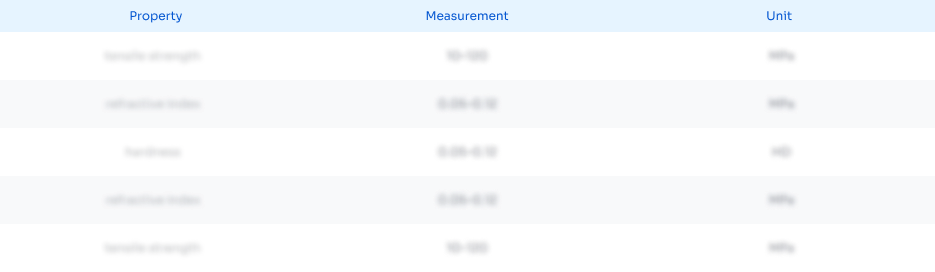
Abstract
Description
Claims
Application Information

- R&D Engineer
- R&D Manager
- IP Professional
- Industry Leading Data Capabilities
- Powerful AI technology
- Patent DNA Extraction
Browse by: Latest US Patents, China's latest patents, Technical Efficacy Thesaurus, Application Domain, Technology Topic, Popular Technical Reports.
© 2024 PatSnap. All rights reserved.Legal|Privacy policy|Modern Slavery Act Transparency Statement|Sitemap|About US| Contact US: help@patsnap.com