Quality control method for numerical-control gas pressure welding of rail
A technology of welding quality and control method, which is applied in the field of welding quality control of barometric pressure welding of rail transit seamless line, can solve problems such as safety hazards of tearing, poor consistency, misjudgment, etc., and achieves reduction of safety hazards and simple and convenient operation , the effect of low skill requirements
- Summary
- Abstract
- Description
- Claims
- Application Information
AI Technical Summary
Problems solved by technology
Method used
Image
Examples
specific Embodiment approach
[0035] A kind of specific embodiment of the present invention is: a kind of rail numerical control air pressure welding quality control method, and its steps are:
[0036] Step a, setting parameters: use welding heat / force simulation test technology to obtain the relationship between temperature-deformation resistance-deformation of the rail to be welded, and then obtain the corresponding pre-compression pressure of the rail in the pre-compression stage according to the welding temperature requirements P 1 , The low-pressure pressure P of the rail in the low-pressure stage 2 , Upsetting pressure P of the rail in the upsetting stage 3 , upsetting amount S 3 , and the oxygen flow rate L 1 and acetylene flow L 2 , pre-pressing heating time τ 1 , preload pressure P 1, Low pressure heating time τ 2 , low pressure P 2 , upsetting time τ 3 , Upsetting pressure P 3 , upsetting amount S 3 , Holding time τ 4 Parameters are preset in the digital controller 9;
[0037] The sp...
Embodiment 2
[0044] The method of this embodiment is basically the same as that of Embodiment 1, the difference is only:
[0045] Step a, when setting parameters: set the preset pre-pressure heating time τ 1 and low pressure heating time τ 2 Respectively changed to the preloading displacement S representing the heating and deformation effects in the preloading stage 1 and the low-pressure displacement S that characterizes the welding heating and deformation effects in the low-pressure stage 2 ;
[0046] Step b, welding heating process control:
[0047] Preloading stage: the preloading displacement S preset in step a by the digital controller 9 1 , preload pressure P 1 , Oxygen flow L 1 and acetylene flow L 2 As the threshold value, corresponding to the real-time displacement signal of the displacement sensor 4 on the welding machine read by the digital controller 9 in real time, the real-time pressure signal of the pressure sensor on the digital control pump station 8, the mass flow...
PUM
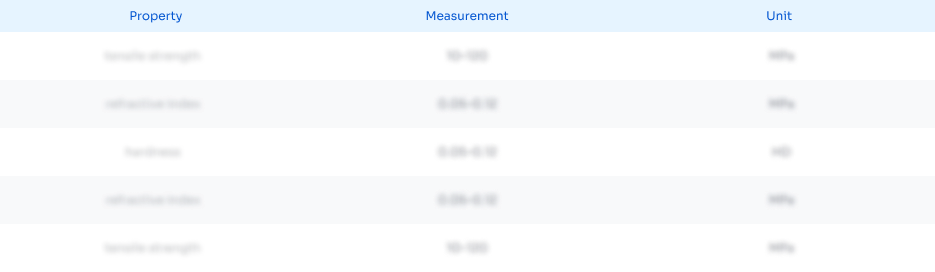
Abstract
Description
Claims
Application Information

- R&D
- Intellectual Property
- Life Sciences
- Materials
- Tech Scout
- Unparalleled Data Quality
- Higher Quality Content
- 60% Fewer Hallucinations
Browse by: Latest US Patents, China's latest patents, Technical Efficacy Thesaurus, Application Domain, Technology Topic, Popular Technical Reports.
© 2025 PatSnap. All rights reserved.Legal|Privacy policy|Modern Slavery Act Transparency Statement|Sitemap|About US| Contact US: help@patsnap.com