Parallel robot with fluid-driven artificial muscle
An artificial muscle, fluid-driven technology, applied in manipulators, manufacturing tools, program-controlled manipulators, etc., can solve the problem of not using flexible artificial muscles to drive parallel robots.
- Summary
- Abstract
- Description
- Claims
- Application Information
AI Technical Summary
Problems solved by technology
Method used
Image
Examples
Embodiment Construction
[0018] Below in conjunction with embodiment 1 of the invention, the operating principle and working process of parallel robot are illustrated:
[0019] The three spaced artificial muscles 9 enter the pressure fluid at the same time, and the other three spaced artificial muscles 9 are squeezed to discharge the fluid, so that the working platform 7 rotates counterclockwise around the vertical spherical universal joint 8 axis; any adjacent two The artificial muscles 9 enter the pressure fluid at the same time, and the rest of the artificial muscles 9 are squeezed to discharge the fluid, which makes the working platform 7 rotate around the horizontal axis determined by the spherical universal joint 8 .
PUM
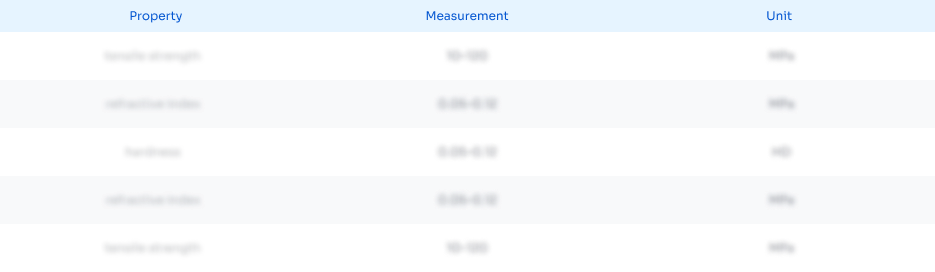
Abstract
Description
Claims
Application Information

- R&D
- Intellectual Property
- Life Sciences
- Materials
- Tech Scout
- Unparalleled Data Quality
- Higher Quality Content
- 60% Fewer Hallucinations
Browse by: Latest US Patents, China's latest patents, Technical Efficacy Thesaurus, Application Domain, Technology Topic, Popular Technical Reports.
© 2025 PatSnap. All rights reserved.Legal|Privacy policy|Modern Slavery Act Transparency Statement|Sitemap|About US| Contact US: help@patsnap.com