Mercerized plush carpet and its weaving method
A carpet and mercerizing technology, applied in the field of mercerized long-haired carpets and its weaving, can solve the problems of dull color, difficulty in cutting pile, hard texture, etc., and achieve the effect of colorful and bright colors and low difficulty in cutting pile
- Summary
- Abstract
- Description
- Claims
- Application Information
AI Technical Summary
Problems solved by technology
Method used
Image
Examples
Embodiment 1
[0020] 1. Twisting and weaving 50 strands of 120D viscose fiber into a thick yarn with a twist of 18 twists;
[0021] 2. Put the above-mentioned viscose fiber yarn in a mixing tank filled with water, the water in the tank shall be able to submerge the above-mentioned viscose fiber yarn, heat to 30°C, and add a dye of 1% of the viscose fiber weight , dyed for 20 minutes, then added viscose weight 5% of the original starch, then heated up to 86 ° C, dyed at this temperature for 30 minutes, stop heating;
[0022] 3. Let go of 75% of the solution in the mixing tank, add water to cool down to 30°C, then add color-fixing agent M with 1% by weight of viscose fiber, and then add silicone oil with 2% by weight of viscose fiber after 20 minutes, and keep at 30°C Temperature for 15 minutes, then rinse the viscose fiber with water, dehydrate, and complete softening and dyeing;
[0023] 4. Drying the dyed viscose fiber, and yarn to form a viscose fiber ply;
[0024] 5. Use 35 pieces of a...
Embodiment 2
[0028] 1. Twist 120 strands of 450D viscose fiber into thick yarn with a twist of 30 twists;
[0029] 2. Put the above-mentioned viscose fiber yarn in a mixing tank filled with water. The water in the tank shall be able to submerge the above-mentioned viscose fiber yarn. Heat it to 35° C., and add 3% of the viscose fiber weight dye , dyed for 25 minutes, then added viscose weight 15% of the original starch, then heated up to 95 ° C, dyed at this temperature for 60 minutes, stop heating;
[0030] 3. Drain 85% of the solution in the mixing tank, add water to cool down to 35°C, then add color-fixing agent M with 3% weight of viscose fiber, and then add silicone oil with 3% weight of viscose fiber after 30 minutes, and keep at 35°C Temperature for 20 minutes, then wash the viscose fiber with water, dehydrate, and complete softening and dyeing;
[0031] 4. Drying the dyed viscose fiber, and yarn to form a viscose fiber ply;
[0032] 5. Use 5 pieces of 10 strands of acrylic strand...
Embodiment 3
[0036] 1. Twist and weave 80 strands of 300D viscose fiber into thick yarn with a twist of 25 twists;
[0037] 2. Put the above-mentioned viscose fiber yarn in a mixing tank filled with water. The water in the tank shall be able to submerge the above-mentioned viscose fiber yarn. Heat it to 32°C and add 2% of the viscose fiber weight dye , dyeing for 23 minutes, then add 10% viscose weight of the original starch, then heat up to 90 ° C, dyeing at this temperature for 45 minutes, stop heating:
[0038] 3. Let go of 80% of the solution in the mixing tank, add water to cool down to 32°C, then add color-fixing agent M with 2% by weight of viscose fiber, and then add silicone oil with 2.5% by weight of viscose fiber after 25 minutes, and keep at 32°C Temperature for 18 minutes, then rinse the viscose fiber with water, dehydrate, and complete softening and dyeing;
[0039] 4. Drying the dyed viscose fiber, and yarn to form a viscose fiber ply;
[0040] 5. Use 20 pieces of 5-strand...
PUM
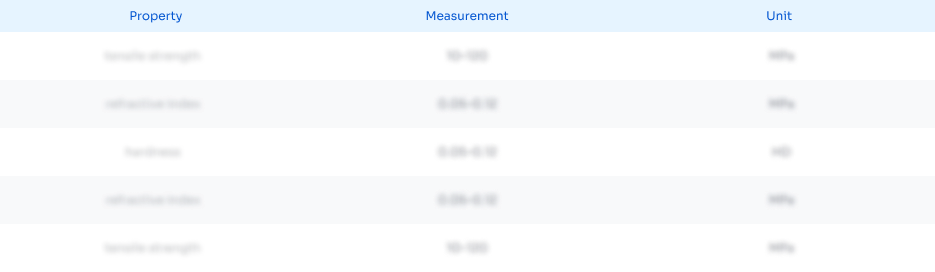
Abstract
Description
Claims
Application Information

- R&D
- Intellectual Property
- Life Sciences
- Materials
- Tech Scout
- Unparalleled Data Quality
- Higher Quality Content
- 60% Fewer Hallucinations
Browse by: Latest US Patents, China's latest patents, Technical Efficacy Thesaurus, Application Domain, Technology Topic, Popular Technical Reports.
© 2025 PatSnap. All rights reserved.Legal|Privacy policy|Modern Slavery Act Transparency Statement|Sitemap|About US| Contact US: help@patsnap.com