Soluble ceramic core for metal casting
A metal casting and ceramic core technology, which is applied in casting equipment, metal processing equipment, casting molten material containers, etc., can solve the problem that the strength of high-purity quartz glass powder ceramic core cannot meet the use requirements and cannot meet the complex cavity of metal castings Forming requirements, difficult to obtain casting cavity and other problems, to achieve the effect of low price, improved adaptability, and convenient strength
- Summary
- Abstract
- Description
- Claims
- Application Information
AI Technical Summary
Problems solved by technology
Method used
Examples
Embodiment 1
[0019] The soluble ceramic mold core for metal casting of the present invention, raw material batching weight percent is composed of:
[0020] Composite powder 85%, silica powder 5%, CMC 10%;
[0021] The compound powder is made by mixing 85% quartz sand and 15% quartz glass.
[0022] Mix the composite material powder evenly and pass through a 100-mesh sieve, take the sieve material, mix it with silicon micropowder and CMC, mix it with 10% wax liquid by weight of the molding material, mix it evenly, put it into the mold and press it to form a core, and demould Afterwards, it is fired at a temperature of 1300±10° C., and naturally cooled to obtain the ceramic core product of the present invention.
[0023] Boil 35% industrial soda ash solution, put the ceramic core in it and cook for 40 minutes, and the core will dissolve.
Embodiment 2
[0025] The soluble ceramic mold core for metal casting of the present invention, raw material batching weight percent is composed of:
[0026] Composite powder 81%, silica powder 8%, CMC 11%;
[0027] The compound powder is made by mixing 85% quartz sand and 15% quartz glass.
[0028] Mix the composite material powder evenly and pass through a 100-mesh sieve, take the sieve material and mix it with silicon micropowder and CMC evenly, mix it with wax liquid with 11% weight of the molding material, mix it evenly, put it into the mold and press it to form a core, and demould Afterwards, it is fired at a temperature of 1200±10° C., and naturally cooled to obtain the ceramic core product of the present invention.
[0029] Boil 35% industrial soda ash solution, put the ceramic core in it and cook for 35 minutes, and the core will dissolve.
Embodiment 3
[0031] The soluble ceramic mold core for metal casting of the present invention, raw material batching weight percent is composed of:
[0032] Composite powder 88%, silica powder 5%, CMC 7%;
[0033] The compound powder is made by mixing 88% quartz sand and 12% quartz glass.
[0034] Mix the composite material powder evenly and pass through a 120-mesh sieve, take the sieve material, mix it with silicon micropowder and CMC, mix it with 10% wax liquid by weight of the molding material, mix it evenly, put it into the mold and press it to form a core, and demould Afterwards, it is fired at a temperature of 1400±10° C., and naturally cooled to obtain the ceramic core product of the present invention.
[0035] Boil 35% industrial soda ash solution, put the ceramic core in it and cook for 40 minutes, and the core will dissolve.
PUM
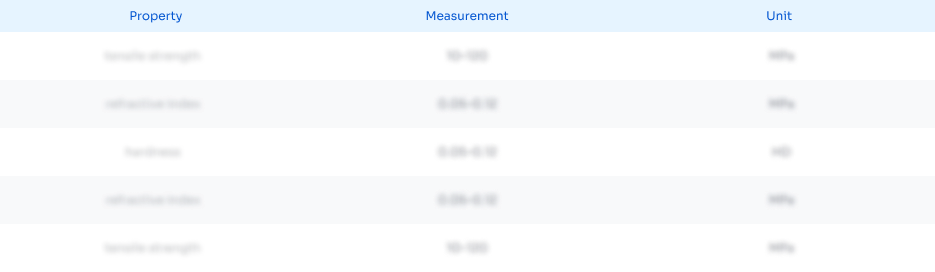
Abstract
Description
Claims
Application Information

- R&D
- Intellectual Property
- Life Sciences
- Materials
- Tech Scout
- Unparalleled Data Quality
- Higher Quality Content
- 60% Fewer Hallucinations
Browse by: Latest US Patents, China's latest patents, Technical Efficacy Thesaurus, Application Domain, Technology Topic, Popular Technical Reports.
© 2025 PatSnap. All rights reserved.Legal|Privacy policy|Modern Slavery Act Transparency Statement|Sitemap|About US| Contact US: help@patsnap.com