Quick forming method by adoption of projection technique
A projection technology and fast technology, applied in the field of manufacturing, can solve the problems of low degree of automation, high cost of use, poor molding accuracy, etc., and achieve the effect of large selection range, convenient control, easy control and adjustment
- Summary
- Abstract
- Description
- Claims
- Application Information
AI Technical Summary
Problems solved by technology
Method used
Image
Examples
Embodiment 1
[0062] The structure of the rapid prototyping machine is as follows figure 2 As shown, load 50kg DuPont SOMOS 6100 photosensitive curing resin in liquid tank 6, load TGC-1 control software in computer 3 (TGC-1 control software flow process is as follows Figure 4 As shown), the digital three-dimensional model 2 of the object can be displayed on the computer monitor; the projector 1 connected to the computer is located above the tray 8, and the photosensitive resin on the tray is provided by the liquid tank 6, in order to keep the photosensitive resin liquid on the tray 6 The distance between the surface 10 and the projector is constant, so that the size of the projection graphics 9 on the photosensitive resin liquid surface remains the same, and the lifting of the tray 8 is adjusted by the lifter 4; a horizontally reciprocating scraper 5 is installed on the liquid tank 6 to ensure The stability of the liquid surface position of the thin layer photosensitive resin and the smoo...
Embodiment 2
[0082] The structure of the rapid prototyping machine and the rapid prototyping method are as in Example 1.
[0083] Projector parameters: Three-chip LCD transmission mode, resolution 800×600, light source 500W, iodine tungsten lamp, wavelength 40nm~800nm.
[0084] Control parameters: Irradiation area: 150mm×150mm
[0085] Forming shape: cube
[0086] Molding size: 100mm×100mm×100mm
[0087] Support size: 100mm×100mm×10mm
[0088] The thickness of each layer in the forming process of the molded object: 0.1mm
[0089] Irradiation times: support 50 times
[0090] The total number of irradiation times for forming entities: 10,000 times
[0091] Each irradiation time: 1.0 seconds
[0092] Test results: Molding time: 270 minutes (including the time required for the leveling action of the layer preparation and the switching of the irradiation pattern)
[0093] Physical size: 99.66mm×9.66mm×99.85mm...
Embodiment 3
[0099] The structure of the rapid prototyping machine and the rapid prototyping method are as in Example 1.
[0100] Projector parameters: Three-chip LCD reflection mode, resolution 1024×768, light source 50W, UHP lamp, wavelength 40nm~800nm.
[0101] Control parameters: Irradiation area: 120mm×120mm
[0102] Forming shape: cube
[0103] Molding size: 100mm×100mm×100mm
[0104] Support size: 100mm×100mm×10mm
[0105] The thickness of each layer in the forming process of the molded object: 0.1mm
[0106] Irradiation times: support 50 times
[0107] The total number of irradiation times for forming entities: 10,000 times
[0108] Each irradiation time: 1.0 seconds
[0109] Test results: Molding time: 386 minutes (including the time required for the leveling action of the layer preparation and the switching of the irradiation pattern)
[0110] Physical size: 99.66mm×9.66mm×99.85mm
[0111]Form...
PUM
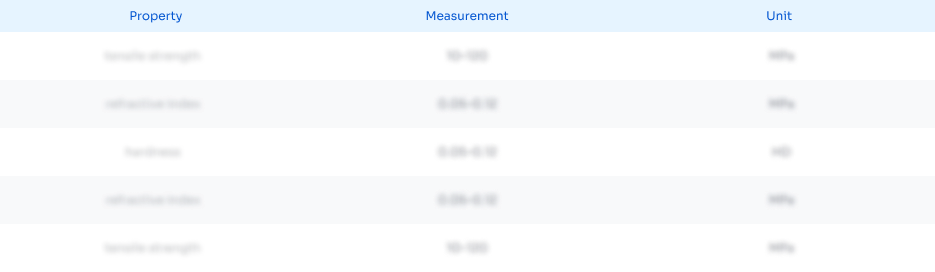
Abstract
Description
Claims
Application Information

- R&D
- Intellectual Property
- Life Sciences
- Materials
- Tech Scout
- Unparalleled Data Quality
- Higher Quality Content
- 60% Fewer Hallucinations
Browse by: Latest US Patents, China's latest patents, Technical Efficacy Thesaurus, Application Domain, Technology Topic, Popular Technical Reports.
© 2025 PatSnap. All rights reserved.Legal|Privacy policy|Modern Slavery Act Transparency Statement|Sitemap|About US| Contact US: help@patsnap.com