Dynamic magnetic synchronous surface motor
A moving magnet and frame technology, applied in the field of moving magnet synchronous surface motors, can solve the problems of air gap magnetic flux density drop and reduce servo operating characteristics, etc.
- Summary
- Abstract
- Description
- Claims
- Application Information
AI Technical Summary
Problems solved by technology
Method used
Image
Examples
Embodiment Construction
[0014] The structural principle and working principle of the present invention will be further described in detail below in conjunction with the accompanying drawings.
[0015] see figure 1 , 2. The present invention includes a frame 1, a stator core 2 with a smooth surface and no slots arranged on the frame 1, and a mover platform 7 floating on the stator core 2, wherein the frame 1 is used as a base for installing the stator core 2 Seat, the upper surface of the stator core 2 and the lower surface of the mover platform 7 are parallel to each other, and there is a thin air gap between them, and the thrust windings 3, 4 and Y in the X direction are respectively arranged on the stator core 2 To the thrust windings 5, 6, and any effective side of the X-direction thrust winding and any effective side of the Y-direction thrust winding are perpendicular to each other, and four Halbach permanent magnet arrays 8 are also arranged on the lower surface of the mover platform 7 , the pe...
PUM
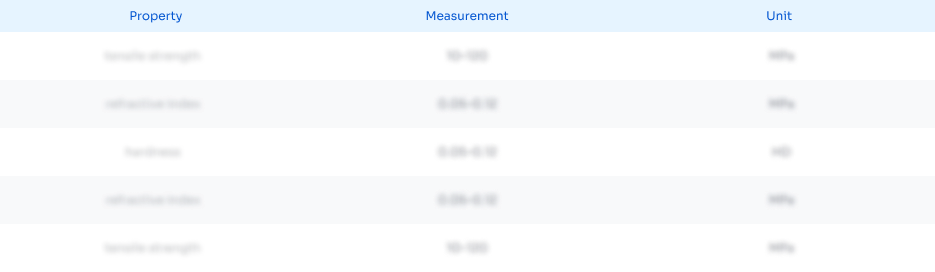
Abstract
Description
Claims
Application Information

- R&D Engineer
- R&D Manager
- IP Professional
- Industry Leading Data Capabilities
- Powerful AI technology
- Patent DNA Extraction
Browse by: Latest US Patents, China's latest patents, Technical Efficacy Thesaurus, Application Domain, Technology Topic, Popular Technical Reports.
© 2024 PatSnap. All rights reserved.Legal|Privacy policy|Modern Slavery Act Transparency Statement|Sitemap|About US| Contact US: help@patsnap.com