Vacuum negative pressure casting process of foam die casting piece
A vacuum negative pressure and casting technology, which is applied in the direction of casting molding equipment, casting molds, manufacturing tools, etc., can solve the problems of unsatisfactory strength and poor finish of castings, and achieve the effects of improving compactness, increasing service life and high strength
- Summary
- Abstract
- Description
- Claims
- Application Information
AI Technical Summary
Problems solved by technology
Method used
Image
Examples
Embodiment
[0018] A vacuum negative pressure casting method for foam plastic mold castings is characterized in that it comprises the following steps:
[0019] ① Fix the model 1 to the suction box 2 first, and the suction box 2 starts to vacuum;
[0020] ②The plastic film 3 is heated and covered on the model 1, and the gate 4 is set on the film 3;
[0021] ③ spray paint layer 5 on the surface of film 3, and dry paint layer 5;
[0022] ④ Place a sand box 7 on the mold plate 6, fill the sand box 7 with dry sand 8, then use a vibrating table 9 to vibrate the sand, and cover the sand box 7 with a sealing film 10;
[0023] ⑤ Vacuumize the sand box 7 so that the surface hardness of the sand mold reaches about 95 (example 90-98), and then the mold is ejected to obtain the cavity;
[0024] ⑥ Obtain the lower cavity according to the same method as above ①~⑤, but there is no gate in step ②;
[0025] ⑦ Combine the upper and lower cavities and cast from the gate 4, while the upper and lower caviti...
PUM
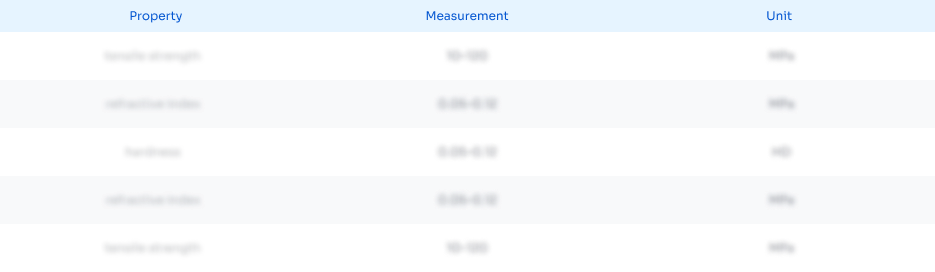
Abstract
Description
Claims
Application Information

- Generate Ideas
- Intellectual Property
- Life Sciences
- Materials
- Tech Scout
- Unparalleled Data Quality
- Higher Quality Content
- 60% Fewer Hallucinations
Browse by: Latest US Patents, China's latest patents, Technical Efficacy Thesaurus, Application Domain, Technology Topic, Popular Technical Reports.
© 2025 PatSnap. All rights reserved.Legal|Privacy policy|Modern Slavery Act Transparency Statement|Sitemap|About US| Contact US: help@patsnap.com