New technique for preparing cellulose carbate through urea embedding method
A technology of carbamate and cellulose, applied in the field of preparing cellulose carbamate, to achieve the effects of good spinnability, low investment cost and shortened production cycle
- Summary
- Abstract
- Description
- Claims
- Application Information
AI Technical Summary
Problems solved by technology
Method used
Image
Examples
Embodiment 1
[0045] After shredding 100 kg of cotton pulp with a degree of polymerization of 621 and adding 1000 L of 15% sodium hydroxide solution into a 2000-liter reactor, turn on the agitator at 30° C. to fully mix the cellulose and sodium hydroxide solution, Stop stirring after 30 minutes, wash with water of the same temperature to remove free lye. After that, add 150 kg of urea to the alkali fiber containing moisture, and fully mix the two in the batching tank. After the urea particles cannot be seen, put the material into the CC synthesis reaction kettle, add 800 kg of inert solvent xylene, and start Stirrer and start to heat up. When the temperature rises to 85°C, there will be distilled matter, and the moisture will be completely removed in nearly 1 hour, and the temperature will quickly rise to 137°C; stop heating after this state lasts for 2 hours, and wait for the temperature to drop to 90°C Stop stirring, recover xylene, then wash the product with hot water at 40°C to separate...
Embodiment 2
[0047] After shredding 100 kg of cotton pulp with a degree of polymerization of 540 and adding 1000 L of 12% sodium hydroxide solution into a 2000-liter reactor, turn on the agitator at 40° C. to fully mix the cellulose and sodium hydroxide solution, After 40 minutes, stop stirring and wash with water of the same temperature to remove free lye. Then add 200 kg of urea to the alkali fiber containing water, mix the two fully in the batching tank, put the material into the CC synthesis reaction kettle after the urea particles are invisible, add 1000 kg of inert solvent xylene, and start Stirrer and start to heat up. When the temperature rises to 85°C, there will be distilled matter, and the moisture will be completely removed in nearly 1 hour, and the temperature will quickly rise to 130°C; stop heating after this state lasts for 2 hours, and wait for the temperature to drop to 90°C Stop stirring, recover xylene, then wash the product with water at a temperature of 50°C to separa...
Embodiment 3
[0049] Add 100kg of cotton linters with a degree of polymerization of 420 and 1000L of 12% sodium hydroxide solution into a 2000-liter reactor, turn on the agitator at 50°C to fully mix the cellulose and sodium hydroxide solution, and stop after 20 minutes Stir and rinse with water of the same temperature to remove free lye. Then add 250 kg of urea to the alkali fiber containing a certain amount of moisture, fully mix the two in the batching tank, put the material into the CC synthesis reaction kettle after the urea particles are invisible, add 1500 kg of inert solvent xylene, Turn on the agitator and start to heat up. When the temperature rises to 85°C, there will be distilled matter, and the moisture will be completely removed in nearly 1 hour, and the temperature will rise to 135°C quickly; stop heating after this state lasts for 2 hours, and wait for the temperature to drop to 90°C Stop stirring at ℃, recycle xylene, then wash the product with water at 70 ℃ to separate it ...
PUM
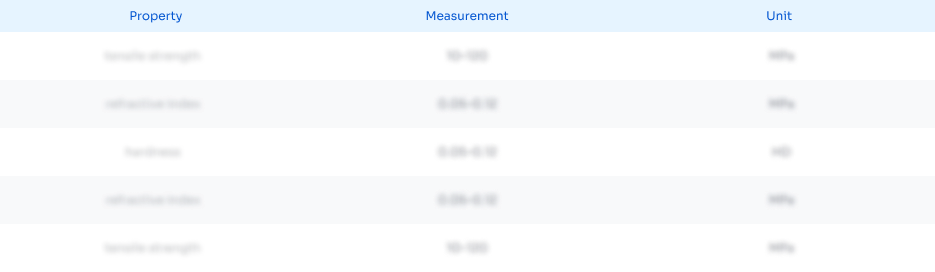
Abstract
Description
Claims
Application Information

- R&D
- Intellectual Property
- Life Sciences
- Materials
- Tech Scout
- Unparalleled Data Quality
- Higher Quality Content
- 60% Fewer Hallucinations
Browse by: Latest US Patents, China's latest patents, Technical Efficacy Thesaurus, Application Domain, Technology Topic, Popular Technical Reports.
© 2025 PatSnap. All rights reserved.Legal|Privacy policy|Modern Slavery Act Transparency Statement|Sitemap|About US| Contact US: help@patsnap.com