Multi-layer coating process to achieve a highly saturated color appearance on a vehicle
A coating and coating technology, which is applied in the field of coating with multi-layer coating, and coating it with multi-layer coating in the initial production stage, which can solve the problems of excess, occupying space, and being expensive.
- Summary
- Abstract
- Description
- Claims
- Application Information
AI Technical Summary
Problems solved by technology
Method used
Image
Examples
Embodiment 1
[0063] Embodiment 1: the preparation of primer
[0064] Prepare the following premix:
[0065] A. Preparation of Iron Oxide Yellow Pigment Dispersion
[0066] The following pigment slurry was prepared: 38.0 g deionized water; 1.0 g acrylic microgel dispersion (as described in Example 4 of patent US4403003); 30.5 g butoxyethanol; 7.5 g Cymel 303 (alkylated melamine formaldehyde resin); 2.0 g of a 10% solution in dimethylethanolamine; and 1.0 g of Surfynol 104 (surfactant). Mix the above components together, then add 20.0g Bayferfox 3910 (yellow iron oxide), the resulting slurry was predispersed with a Cowles paddle. The mixture is then milled in a horizontal ball mill until the desired particle size of less than 0.5 microns is achieved.
[0067] B. Preparation of Iron Oxide Yellow Pigment Dispersion
[0068] The following pigment slurry was prepared: 7.0 g deionized water; 10.0 g acrylic microgel dispersion (as described in Example 4 of patent US4403003); 10.0 g but...
Embodiment 2
[0087] Embodiment 2: prepare water-based red effect color primer layer (the first primer layer) composition
[0088] A water-based red effect color primer layer composition is prepared by mixing the following ingredients with continuous agitation: 1.A. Acrylic microgel dispersion as described, greater than 15.7 parts; 1.I. Black pigment dispersion as described, Greater than 1.6 parts; magenta pigment dispersion as described in 1.F., greater than 15.5 parts; red pigment dispersion as described in 1.G., greater than 30.2 parts; Cymel 303, 1.7 parts; 1.C. Effect pigment concentrate "C" (Xirallic ), more than 15.3 parts; 1.D. Effect pigment concentrate "D" (Iriodin ), greater than 8.1 parts; 1.k. rheological base material described, greater than 9.0 parts; Surfynol 104, 1.0 servings. Adjust to reach required viscosity (when shear rate D=1 / second, viscosity is 2000-4000mPas) and pH value (pH value is 8.2-8.8) by adjusting with appropriate composition, and this compositio...
Embodiment 3
[0089] Embodiment 3: prepare water-based red solid color primer layer (the first primer layer) composition
[0090] A waterborne red solid color primer layer composition was prepared by mixing the following ingredients with constant agitation: 1.A. Acrylic microgel dispersion as described, greater than 36.5 parts; 1.E. Red pigment dispersion as described, greater than 22.8 parts; 1.J, red pigment dispersion as described, more than 11.4 parts; 1.H. yellow pigment dispersion as described, more than 5.3 parts; 1.B. red pigment dispersion as described, more than 3.4 parts ; 1.A. Yellow pigment dispersion as described, greater than 2.3 parts; Cymel 303, 5.3 parts; rheological base material described by 1.K., greater than 9.2 parts; Surfynol 104, 1.8 servings. Adjust to reach required viscosity (when shear rate D=1 / second, viscosity is 2000-4000mPas) and pH value (pH value is 8.2-8.8) by adjusting with appropriate composition, and this composition contains: deionized water , ...
PUM
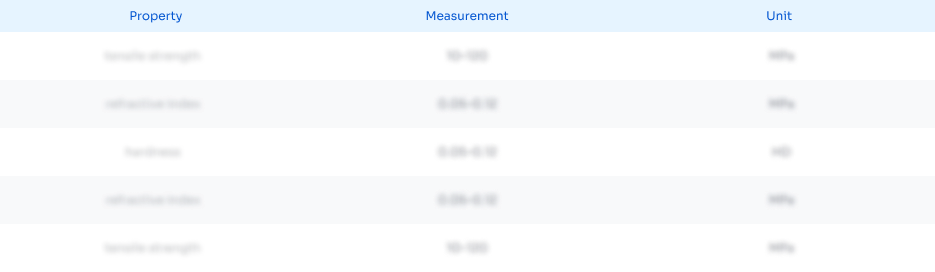
Abstract
Description
Claims
Application Information

- R&D Engineer
- R&D Manager
- IP Professional
- Industry Leading Data Capabilities
- Powerful AI technology
- Patent DNA Extraction
Browse by: Latest US Patents, China's latest patents, Technical Efficacy Thesaurus, Application Domain, Technology Topic, Popular Technical Reports.
© 2024 PatSnap. All rights reserved.Legal|Privacy policy|Modern Slavery Act Transparency Statement|Sitemap|About US| Contact US: help@patsnap.com