Method for preparing o-chloroaniline
A technology for o-chloroaniline and o-chloronitrobenzene is applied in the field of liquid-phase catalytic hydrogenation of o-chloronitrobenzene to produce o-chloroaniline, and can solve the problems of lowering product quality, increasing production cost, serious dechlorination, etc. Low, dehydrogenation inhibition, high yield effect
- Summary
- Abstract
- Description
- Claims
- Application Information
AI Technical Summary
Benefits of technology
Problems solved by technology
Method used
Examples
Embodiment 1
[0012] In a 100ml stainless steel high-pressure reactor, add 2g of o-chloronitrobenzene, 0.45g of Ru / C catalyst, 30ml of ethanol solution with a mass percentage of 95%, close the reactor, replace the air with nitrogen for 3 times, start stirring, and heat up to 210 ℃, reacted for 6 hours, stopped the reaction, took out the reaction solution, filtered out the catalyst, and the filtrate was analyzed by gas chromatography for the content of each component. The results showed that the conversion rate of o-chloronitrobenzene was 91.6%, and the selectivity of o-chloroaniline was 88.7%. %.
Embodiment 2
[0014] In a 100ml stainless steel high-pressure reactor, add 2g o-chloronitrobenzene, 0.45g Ru / C catalyst, 30ml mass percentage is 95% ethanol solution, close the reactor, replace the air with nitrogen for 3 times, start stirring, and heat up to 180°C , reacted for 6 hours, stopped the reaction, took out the reaction solution, filtered out the catalyst, and the filtrate was analyzed by gas chromatography for the content of each component. The results showed that the conversion rate of o-chloronitrobenzene was 26.2%, and the selectivity of o-chloroaniline was 97.4%. .
Embodiment 3
[0016] In a 100ml stainless steel high-pressure reactor, add 2g o-chloronitrobenzene, 0.45g NiB amorphous catalyst, 30ml mass percent as 95% ethanol solution, close the reactor, replace the air with nitrogen for 3 times, start stirring, and heat up to 210 DEG C, reacted for 6 hours, stopped the reaction, took out the reaction solution, filtered out the catalyst, and the filtrate was analyzed by gas chromatography for the content of each component. The results showed that the conversion rate of o-chloronitrobenzene was 22.1%, and the selectivity of o-chloroaniline was 89.7%.
PUM
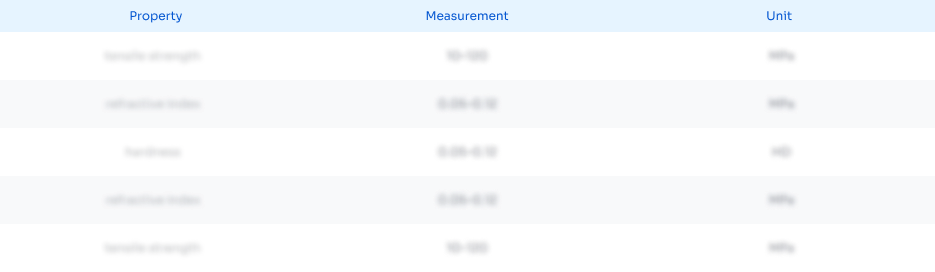
Abstract
Description
Claims
Application Information

- R&D
- Intellectual Property
- Life Sciences
- Materials
- Tech Scout
- Unparalleled Data Quality
- Higher Quality Content
- 60% Fewer Hallucinations
Browse by: Latest US Patents, China's latest patents, Technical Efficacy Thesaurus, Application Domain, Technology Topic, Popular Technical Reports.
© 2025 PatSnap. All rights reserved.Legal|Privacy policy|Modern Slavery Act Transparency Statement|Sitemap|About US| Contact US: help@patsnap.com