Nomex fibre surface modifying method
A polyaramid fiber and surface modification technology, applied in the field of surface modification of polyaramid fiber, can solve the problems of complicated operation, uneven performance and high cost
- Summary
- Abstract
- Description
- Claims
- Application Information
AI Technical Summary
Problems solved by technology
Method used
Image
Examples
Embodiment 1
[0078] Evenly cut 80 cm long Kevlar29 fiber, 1500 denier. Air-dried at room temperature and weighed.
[0079] Weigh a certain amount of 2,4-toluene diisocyanate and pour it into a beaker, the amount is based on the amount that can completely immerse the fiber, and heat the solution to 70°C. After the temperature is constant, put the fiber in a beaker in a natural state, and make it completely immersed in 2,4-toluene diisocyanate, react for 1 hour, take out the fiber, and wash it twice with deionized water and anhydrous acetone in turn , dry with cold air, and after the weight is constant, measure the strength of the modified fiber, the bonding strength between the modified fiber and epoxy resin, and the water absorption of the modified fiber after being boiled at 95°C for 10 hours and 95°C Fiber strength after boiling for 10 hours and 55 hours.
Embodiment 2
[0081] As described in Example 1, the temperature was increased to 80° C., and the rest of the operations were unchanged.
Embodiment 3
[0083] As described in Example 1, the temperature was increased to 90° C., and the rest of the operations were unchanged.
[0084] The water absorption data and fiber strength data of the modified fibers obtained in Examples 1, 2, and 3 were compared with those of unmodified fibers. The comparison of water absorption is shown in Table 1.
[0085] Processing temperature
unmodified fiber
70℃
80℃
90℃
Water absorption at 95°C for 10 hours
3.50%
0.75%
0.81%
1.10%
Decrease rate of fiber water absorption after modification
-
78.5%
76.8%
68.6%
[0086] The strength of the modified fiber and the comparison of the strength after water absorption are shown in Table 2.
[0087] Processing temperature
unmodified fiber
70℃
80℃
90℃
treated fiber * intensity
(cN)
31.1
29.3
28.8
29.1
...
PUM
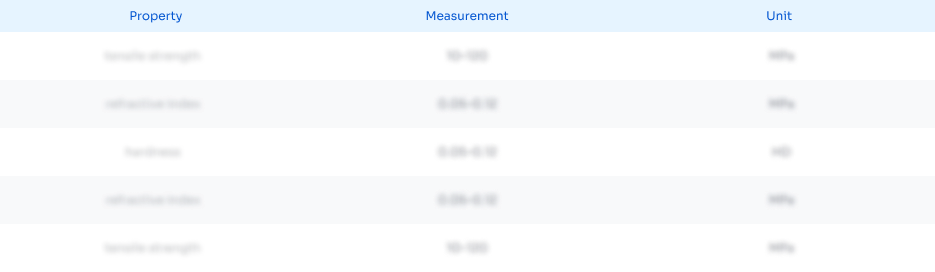
Abstract
Description
Claims
Application Information

- R&D
- Intellectual Property
- Life Sciences
- Materials
- Tech Scout
- Unparalleled Data Quality
- Higher Quality Content
- 60% Fewer Hallucinations
Browse by: Latest US Patents, China's latest patents, Technical Efficacy Thesaurus, Application Domain, Technology Topic, Popular Technical Reports.
© 2025 PatSnap. All rights reserved.Legal|Privacy policy|Modern Slavery Act Transparency Statement|Sitemap|About US| Contact US: help@patsnap.com