Apparatus and method for treating incineration exhaust gas of dry-wet mixed solid waste
A solid waste and tail gas treatment technology, applied in combustion methods, separation methods, chemical instruments and methods, etc., can solve the problems of low pollutant removal rate, high investment and operating costs, and achieve inhibition of dioxin generation and improvement. Absorption efficiency, fouling avoidance effect
- Summary
- Abstract
- Description
- Claims
- Application Information
AI Technical Summary
Problems solved by technology
Method used
Image
Examples
example 1
[0037] Example 1: The 180°C flue gas from the incinerator enters the flue gas reheater, and the temperature drops to 150°C. In the outlet flue of the flue gas reheater, spray activated carbon adsorbent, and the adsorbent comes from the adsorbent storage tank 11. The activated carbon is fully mixed with the flue gas, and enters the evaporative cooler 1 after 2 to 3 seconds. In the evaporative cooler 1, an atomizing nozzle 15 is arranged, and the absorption slurry coming from the settling tank 6 enters the evaporative cooler 1 by the jet pump 7, and mixes with the flue gas after atomization, so that the flue gas is rapidly cooled to 125°C, and then enters the evaporative cooler 1. Bag filter reactor 2. The ash removed by the evaporative cooler 1 and the bag filter reactor 2 enters the ash storage tank 3 . The flue gas from the bag filter reactor 2 enters the bubbling fluidized reactor 5 . The absorption liquid in the bubbling fluidized reactor 5 is sprayed by the circulation p...
example 2
[0038] Example 2: The 160°C flue gas from the incinerator enters the flue gas reheater, and the temperature drops to 130°C. In the outlet flue of the flue gas reheater, activated carbon adsorbent is sprayed, and the adsorbent comes from the adsorbent storage tank 11. The activated carbon is fully mixed with the flue gas, and enters the evaporative cooler 1 after 2 to 3 seconds. In the evaporative cooler 1, an atomizing nozzle 15 is arranged, and the absorption slurry coming from the settling tank 6 enters the evaporative cooler 1 by the jet pump 7, and mixes with the flue gas after atomization, so that the flue gas rapidly cools down to 110°C, and then enters the evaporative cooler 1. Bag filter reactor 2. The ash removed by the evaporative cooler 1 and the bag filter reactor 2 enters the ash storage tank 3 . The flue gas from the bag filter reactor 2 enters the bubbling fluidized reactor 5 . The absorption liquid in the bubbling fluidized reactor 5 is sprayed by the circula...
PUM
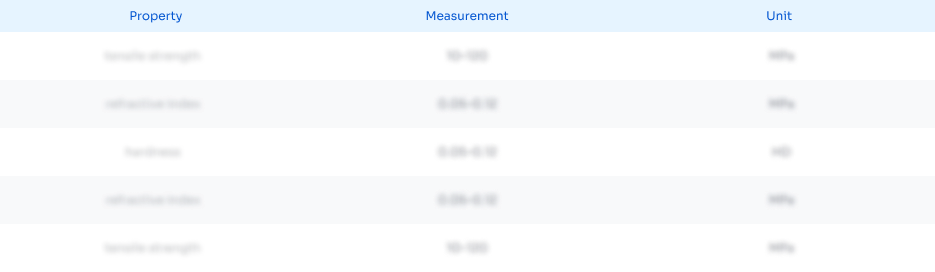
Abstract
Description
Claims
Application Information

- Generate Ideas
- Intellectual Property
- Life Sciences
- Materials
- Tech Scout
- Unparalleled Data Quality
- Higher Quality Content
- 60% Fewer Hallucinations
Browse by: Latest US Patents, China's latest patents, Technical Efficacy Thesaurus, Application Domain, Technology Topic, Popular Technical Reports.
© 2025 PatSnap. All rights reserved.Legal|Privacy policy|Modern Slavery Act Transparency Statement|Sitemap|About US| Contact US: help@patsnap.com