Thermoplastic resin base carbon fiber composite material, and its manufacturing method and apparatus
A thermoplastic resin and composite material technology, applied in the field of building reinforcement materials, can solve the problems of restricting the development of thermoplastic composite materials, difficult impregnation of reinforcing fibers, high viscosity, etc., and achieve the improvement of comprehensive performance, heat distortion temperature, and environmental pressure reduction. Effect
- Summary
- Abstract
- Description
- Claims
- Application Information
AI Technical Summary
Problems solved by technology
Method used
Image
Examples
Embodiment Construction
[0017] Such as figure 1 As shown, the resin matrix of the thermoplastic resin-based continuous carbon fiber composite material sheet is thermoplastic resin (TEEK).
[0018] Such as figure 1 , figure 2 As shown, this product is molded in two steps. In the first step, the high-viscosity thermoplastic resin solution is coated on the surface of the carbon fiber, and prefabricated into a strip-shaped thin-layer prepreg. Sheet, extruded thermoplastic resin coated on carbon fiber, then impregnated, rolled and shaped, after natural cooling, drawn and rolled. In the second step, the multi-layered prepreg is pultruded into the final product; the specific steps are: preheating, hot pressing, forming and then cooling and setting, winding, Traction, to get the finished product. Prepare a TEEK resin continuous carbon fiber prepreg tape with a thickness of about 0.5mm, and the carbon fiber volume fraction should be greater than 60%. The number of laminated layers of prepreg tape is det...
PUM
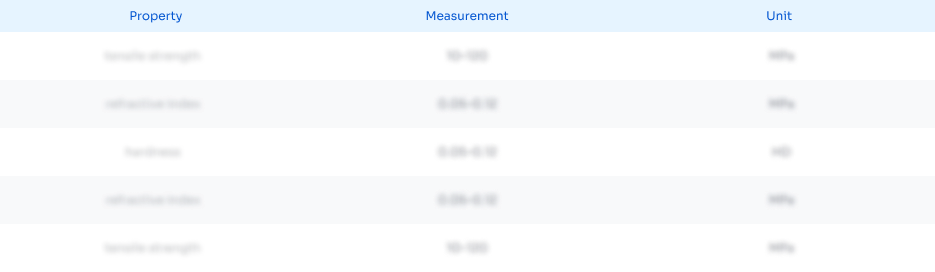
Abstract
Description
Claims
Application Information

- R&D Engineer
- R&D Manager
- IP Professional
- Industry Leading Data Capabilities
- Powerful AI technology
- Patent DNA Extraction
Browse by: Latest US Patents, China's latest patents, Technical Efficacy Thesaurus, Application Domain, Technology Topic, Popular Technical Reports.
© 2024 PatSnap. All rights reserved.Legal|Privacy policy|Modern Slavery Act Transparency Statement|Sitemap|About US| Contact US: help@patsnap.com