Process for preparing alpha-semi-hydrated gypsum from modified gypsum at normal pressure
A technology of gypsum and hemihydrate gypsum, applied in the direction of calcium/strontium/barium sulfate, etc., can solve the problems of large capital increase, high production cost, complicated equipment, etc.
- Summary
- Abstract
- Description
- Claims
- Application Information
AI Technical Summary
Problems solved by technology
Method used
Image
Examples
Embodiment 1
[0026] Crush raw gypsum to a certain particle size, add a certain proportion of salt solution to the slurry mixing tank, and prepare a slurry with a concentration of about 10-20%, the total concentration of the crystallization agent is 10%, and the composition is: CaCl 2 0.1%, MgCl 2 1%, KCl4.9%, Borax 4%. After mixing evenly, heat up to 90°C through a heat exchanger and enter the crystallizer for a residence time of 2 to 4 hours while stirring. After the crystal form changes, it enters the downcomer and is sent to the product tank at the lower part. The temperature in the product tank is continuously controlled at 90°C to make the crystal continue to grow. Monitor slurry density > 1000Kg / m 3 Finally, extract the slurry and send it to the cyclone to separate the solid and liquid. The large crystals in the lower part can be separated by centrifugation, washed with fresh water, sent to the boiling dryer for drying, and then transported and packaged. The slurry containing smal...
Embodiment 2
[0028]Crush the raw gypsum to a certain particle size, add a certain ratio of salt solution to the slurry tank, and prepare a slurry with a concentration of about 10-20%. The total concentration of the crystallization agent is 15%, and the composition is: CaCl 2 5%, MgCl 2 10%, KCl3%, Borax 2%. After mixing evenly, heat up to 95°C through a heat exchanger and enter the crystallizer for a residence time of 2 to 4 hours while stirring. When the crystal form changes, it enters the downcomer and is sent to the lower product tank. The temperature in the product tank is continuously controlled at 95°C to make the crystal continue to grow. Monitor slurry density > 1000Kg / m 3 Finally, extract the slurry and send it to the cyclone to separate the solid and liquid. The large crystals in the lower part can be separated by centrifugation, washed with fresh water, sent to the boiling dryer for drying, and then transported and packaged. The slurry containing small particles separated fro...
Embodiment 3
[0030] Crush raw gypsum to a certain particle size, add a certain ratio of salt solution to the slurry mixing tank, and prepare a slurry with a concentration of about 10-20%. The total concentration of the crystallization agent is 20%, and the composition is: CaCl 2 5%, MgCl 2 5%, KCl5%, borax 5%. After mixing evenly, heat up to 90°C through a heat exchanger and enter the crystallizer for a residence time of 2 to 4 hours while stirring. After the crystal form changes, it enters the downcomer and is sent to the product tank at the lower part. The temperature in the product tank is continuously controlled at 90°C to make the crystal continue to grow. Monitor slurry density > 1000Kg / m 3 Finally, extract the slurry and send it to the cyclone to separate the solid and liquid. The large crystals in the lower part can be separated by centrifugation, washed with fresh water, sent to the boiling dryer for drying, and then transported and packaged. The slurry containing small particl...
PUM
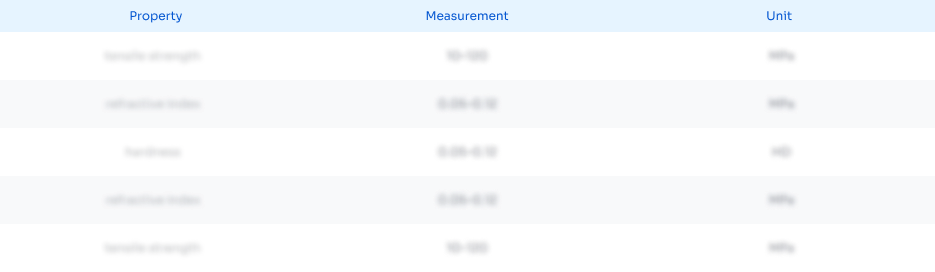
Abstract
Description
Claims
Application Information

- R&D
- Intellectual Property
- Life Sciences
- Materials
- Tech Scout
- Unparalleled Data Quality
- Higher Quality Content
- 60% Fewer Hallucinations
Browse by: Latest US Patents, China's latest patents, Technical Efficacy Thesaurus, Application Domain, Technology Topic, Popular Technical Reports.
© 2025 PatSnap. All rights reserved.Legal|Privacy policy|Modern Slavery Act Transparency Statement|Sitemap|About US| Contact US: help@patsnap.com