Equipment for manufacturing steel plastic pipe
A technology for manufacturing equipment and steel-plastic pipes, which is applied in the field of improved steel-plastic pipe manufacturing equipment, can solve the problems of pipe falling and pipe top deviation, and achieve the effect of preventing arching and maintaining normal working conditions.
- Summary
- Abstract
- Description
- Claims
- Application Information
AI Technical Summary
Problems solved by technology
Method used
Image
Examples
Embodiment 1
[0017] Example 1. See figure 1 , Figure 2, the steel-plastic pipe manufacturing equipment of this example has a furnace 1 for heating the pipe, 16.2m in length, 1.7m in height and 1.7m in width, one end of the furnace has a rear top cylinder 2, and the other end has a coaxial injection molding machine 3 with holes The head angle of injection machine head 3-1 is 120 ° (seeing Fig. 3) and stretches into furnace wall. Establish four fork frames 4 that can be lifted under the axis, and there are pulleys 4-1 at the bottom of the fork frames to cooperate with the cam mechanism 5 fixed on the outer bottom of the furnace, and the nearest one is 20 cm away from the injection machine head. There is a sprocket device on one side of the furnace, the outside is matched with the assembly line, and the side is adapted to the horizontal guide rail 18. There are symmetrical square guide rails 9 on both sides of the sprocket device. There is a square steel body 6 at the bottom of the device, a...
PUM
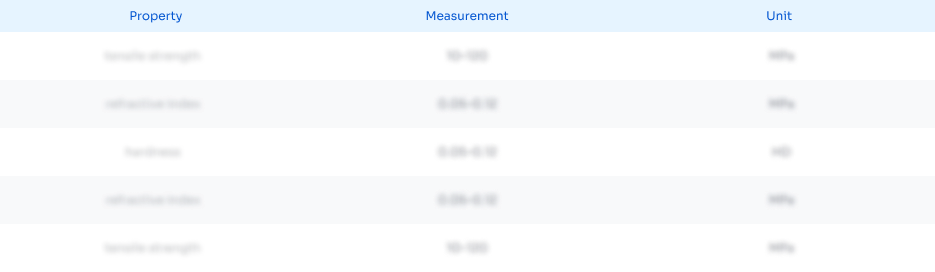
Abstract
Description
Claims
Application Information

- R&D
- Intellectual Property
- Life Sciences
- Materials
- Tech Scout
- Unparalleled Data Quality
- Higher Quality Content
- 60% Fewer Hallucinations
Browse by: Latest US Patents, China's latest patents, Technical Efficacy Thesaurus, Application Domain, Technology Topic, Popular Technical Reports.
© 2025 PatSnap. All rights reserved.Legal|Privacy policy|Modern Slavery Act Transparency Statement|Sitemap|About US| Contact US: help@patsnap.com