Production process for separating ethylbenzene and ortho-xylene from mixed xylene
A technology for mixing xylene and production process, which is applied in the purification/separation of hydrocarbons, hydrocarbons, chemical instruments and methods, etc., can solve the problems of large catalyzing dose, large equipment investment, high energy consumption, and achieves moderate separation conditions, The effect of good air flux and lower energy consumption
- Summary
- Abstract
- Description
- Claims
- Application Information
AI Technical Summary
Problems solved by technology
Method used
Image
Examples
Embodiment 1
[0024] Add xylene raw material D and 2% volume ratio catalyst H in mixer 1, stir evenly at normal temperature, and dissolve each other; After mixing, enter o-xylene separation tower 2 equipped with stainless steel wire corrugated packing at 7L / h, tower The temperature of the kettle is 149°C, the pressure of the tower kettle is ≤0.02Mpa, and the reflux ratio at the top of the tower is 15.3. The ortho-xylene product E is separated from the tower kettle, and part E is reboiled by the tower kettle reboiler 6, and returns to the o-xylene separation tower 2 , the tower overhead steam A contains catalyst, ethylbenzene, p-xylene, m-xylene; the tower overhead steam A enters the tower top reflux intermediate tank 4 after being cooled by the cooler 3, and a part of it is injected into the tower top reflux intermediate tank 4 through the pump 5 as reflux Part of the top of the o-xylene separation tower 2 is used as distillate A; distillate A enters the ethylbenzene separation tower 7 at 4L...
Embodiment 4
[0027]Add xylene raw material D and 4% volume ratio catalyst H in mixer 1, stir evenly at normal temperature, and dissolve each other; After mixing, enter o-xylene separation tower 2 equipped with stainless steel wire corrugated packing at 6L / h, tower The temperature of the kettle is 140°C, the pressure of the tower kettle is ≤0.02Mpa, and the top reflux ratio is 16. The ortho-xylene product E is separated from the tower kettle. The output steam A contains catalyst, ethylbenzene, p-xylene, and m-xylene; the steam A distilled from the tower top is cooled by the cooler 3 and enters the top reflux intermediate tank 4, and a part of it is pumped into the o-xylene as reflux through the pump 5. The top of the xylene separation tower 2, a part is used as distillate A; distillate A enters the catalyst recovery tower 12, the temperature of the tower bottom is controlled at 130 ° C, the pressure of the tower bottom is ≤ 0.01Mpa, the top reflux ratio is 8, and the tower bottom is separate...
Embodiment 5
[0029] The steps and the volume ratio of the catalyst are the same as in Example 4, and its rectification conditions: feed rate 15L / h, 160°C of tower bottom temperature of o-xylene separation tower 2, tower bottom pressure≤0.02Mpa, top reflux ratio of 16 ; The temperature of the tower bottom of the catalyst recovery tower 12 is 160° C., the pressure of the tower bottom is ≤0.01Mpa, and the reflux ratio at the top of the tower is 8.
PUM
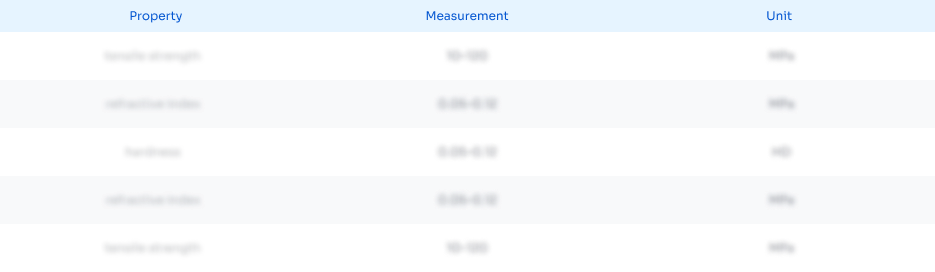
Abstract
Description
Claims
Application Information

- R&D
- Intellectual Property
- Life Sciences
- Materials
- Tech Scout
- Unparalleled Data Quality
- Higher Quality Content
- 60% Fewer Hallucinations
Browse by: Latest US Patents, China's latest patents, Technical Efficacy Thesaurus, Application Domain, Technology Topic, Popular Technical Reports.
© 2025 PatSnap. All rights reserved.Legal|Privacy policy|Modern Slavery Act Transparency Statement|Sitemap|About US| Contact US: help@patsnap.com