Preparation technology of ving/polymer/modified montmorillonoid nano composite tanoing agent
A vinyl polymer, compound tanning agent technology, applied in animal husbandry, chemical treatment of small raw hides/large raw hides/leather hides/furs, applications, etc., to achieve good water vapor permeability, high exhaustion rate, and obvious thickening. Effect
- Summary
- Abstract
- Description
- Claims
- Application Information
AI Technical Summary
Problems solved by technology
Method used
Examples
Embodiment 1
[0018] Embodiment 1,1) hexadecyltrimethylammonium bromide modified montmorillonite: first montmorillonite is added to deionized water with a mass percentage of 5%, stirring makes montmorillonite form a uniform colloidal liquid, Ultrasonic treatment for 60 minutes, then add cetyltrimethylammonium bromide measured at 90mmol / 100g montmorillonite; stir at 90°C for 2 hours, and finally use ultrasonic treatment for 30 minutes again to obtain hexadecyl trimethylammonium bromide Trimethyl ammonium bromide modified montmorillonite;
[0019] 2) Preparation of vinyl polymer: first, acrylic acid, acrylonitrile, ethyl acrylate and isopropanol are mixed and dissolved in deionized water to make acrylic acid containing 8% by mass, 12% acrylonitrile, 1% A mixed solution of ethyl acrylate and 1% isopropanol, add half of the mixed solution into deionized water with a total mass of 78% of the mixed solution. , 10% of the total mass of acrylonitrile and isopropanol is 10% water-soluble initiator ...
Embodiment 2
[0022]Embodiment 2: 1) hexadecyltrimethylammonium bromide modified montmorillonite: first montmorillonite is added to deionized water with a mass percentage of 15%, stirring makes montmorillonite form a uniform colloidal liquid, Treat with ultrasonic wave for 45 minutes, then add hexadecyltrimethylammonium bromide measured by 110mmol / 100g montmorillonite; stir at 70°C for 3 hours, and finally treat with ultrasonic wave for 55 minutes again, which is hexadecyl trimethylammonium bromide Trimethyl ammonium bromide modified montmorillonite;
[0023] 2) Preparation of vinyl polymer: first, acrylic acid, acrylonitrile, ethyl acrylate and isopropanol are mixed and dissolved in deionized water to make acrylic acid containing 12% by mass, 10% acrylonitrile, 1.2% A mixed solution of ethyl acrylate and 1.8% isopropanol, add half of the mixed solution into deionized water with 75% of the total mass of the mixed solution. The concentration of 8% of the total mass of acrylonitrile and isop...
Embodiment 3
[0026] Embodiment 3: 1) hexadecyltrimethylammonium bromide modified montmorillonite: first montmorillonite is added to deionized water with 8% mass percentage, stirring makes montmorillonite form a uniform colloidal liquid, Treat with ultrasonic wave for 30 minutes, then add cetyltrimethylammonium bromide measured at 100mmol / 100g montmorillonite; stir at 85°C for 4 hours, and finally treat with ultrasonic wave for 40 minutes again, which is hexadecyl Trimethyl ammonium bromide modified montmorillonite;
[0027] 2) Preparation of vinyl polymer: first, acrylic acid, acrylonitrile, ethyl acrylate and isopropanol are mixed and dissolved in deionized water to make acrylic acid containing 9% by mass, 11% acrylonitrile, 1.5% A mixed solution of ethyl acrylate and 4% isopropanol, add half of the mixed solution into deionized water with a total mass of 74.5% of the mixed solution. , 4% of the total mass of acrylonitrile and isopropanol is a 10% water-soluble initiator ammonium persulf...
PUM
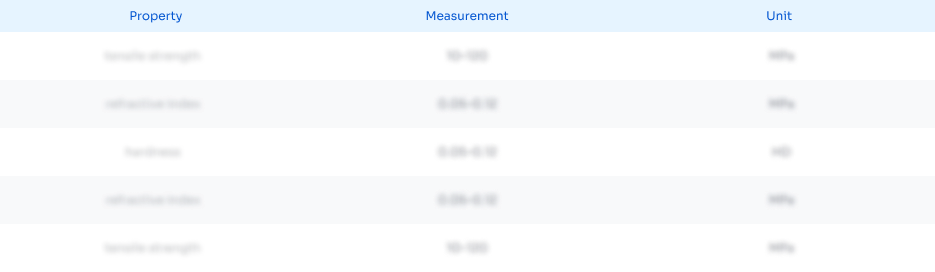
Abstract
Description
Claims
Application Information

- Generate Ideas
- Intellectual Property
- Life Sciences
- Materials
- Tech Scout
- Unparalleled Data Quality
- Higher Quality Content
- 60% Fewer Hallucinations
Browse by: Latest US Patents, China's latest patents, Technical Efficacy Thesaurus, Application Domain, Technology Topic, Popular Technical Reports.
© 2025 PatSnap. All rights reserved.Legal|Privacy policy|Modern Slavery Act Transparency Statement|Sitemap|About US| Contact US: help@patsnap.com