Burning chamber of IC engine
A technology for combustion chambers and internal combustion engines, applied to internal combustion piston engines, combustion engines, mechanical equipment, etc., can solve the problems of unevenness, short penetrating distance of umbrella-shaped spray, and too thick circular distribution of mixed gas, so as to achieve fast spray dispersion speed, Large spatial range of distribution and improvement of emission indicators
- Summary
- Abstract
- Description
- Claims
- Application Information
AI Technical Summary
Problems solved by technology
Method used
Image
Examples
Embodiment Construction
[0010] exist figure 1 , In the embodiment shown in 2, in the combustion chamber (5) that is made up of cylinder head (1), piston (2) and cylinder liner (3), be provided with 6 spray collisions on the inner wall of combustion chamber (5) ridge (2a), the 6 mist oil beams (6) sprayed out by the injector (4) are just facing the 6 collision ridges (2a), because the collision ridge (2a) has a profile suitable for spray flow, in the main During the upward movement of the piston (2) in the oil injection stage, each oil beam falls on the top, middle, and bottom of the collision ridge in turn, part of the spray is rebounded, and part of the spray is quickly dispersed along the guiding arcs on both sides of the collision ridge, realizing the secondary Atomization.
PUM
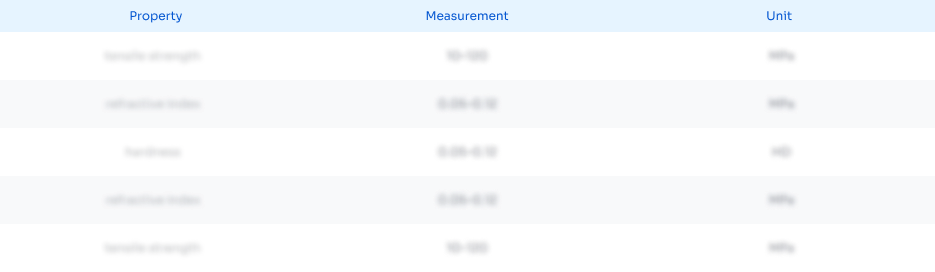
Abstract
Description
Claims
Application Information

- R&D
- Intellectual Property
- Life Sciences
- Materials
- Tech Scout
- Unparalleled Data Quality
- Higher Quality Content
- 60% Fewer Hallucinations
Browse by: Latest US Patents, China's latest patents, Technical Efficacy Thesaurus, Application Domain, Technology Topic, Popular Technical Reports.
© 2025 PatSnap. All rights reserved.Legal|Privacy policy|Modern Slavery Act Transparency Statement|Sitemap|About US| Contact US: help@patsnap.com