Catalyst component for olefin polymerization reaction and catalyst
A technology for olefin polymerization and catalyst, which is applied in the field of catalyst components and catalysts for olefin polymerization, and can solve the problems of narrow molecular weight distribution of polymers and unfavorable polymer development.
- Summary
- Abstract
- Description
- Claims
- Application Information
AI Technical Summary
Problems solved by technology
Method used
Image
Examples
Embodiment 1
[0049] Example 1 Preparation of 2,2-dimethyl-1,5-pentanediol dibenzoate
[0050] (1) Preparation of 2,2-dimethylglutarate diethyl ether
[0051] Add 0.3 mol of ethanol, 40 ml of toluene and 0.4 ml of concentrated sulfuric acid to 0.1 mol of 2,2-dimethylglutaric acid, stir and mix well, then heat to reflux. Use a water separator to remove water until the separated water reaches the theoretically calculated amount to stop the reaction. Neutralize with saturated sodium carbonate solution, extract with ethyl acetate, separate the upper layer solution, wash with saturated saline solution until neutral, and dry over anhydrous sodium sulfate. The solvent was removed and distilled under reduced pressure to obtain colorless liquid 2,2-dimethylglutaric acid diethyl ester with a yield of 90%. 1 HNMR (TMS, CDCl 3 , ppm): δ1.18 (6H, s, methyl H), 1.23 ~ 1.27 (6H, t, methyl H of ethanol), 1.7 ~ 1.8 (2H, t, methylene H), 2.25 ~ 2.29 ( 2H, t, methylene H), 4.0 ~ 4.1 (4H, m, methylene H of...
Embodiment 2
[0056] Embodiment 2: 1, the preparation of 1-dibenzoyloxyethyl cyclohexane
[0057] (1) Preparation of 1,1-diathanol diethyl cyclohexane
[0058] Add 0.3 mol of ethanol, 40 ml of toluene and 0.4 ml of concentrated sulfuric acid to 0.1 mol of 1,1-diacetate cyclohexane, stir and mix well, then heat to reflux. Use a water separator to remove water until the separated water reaches the theoretically calculated amount to stop the reaction. Neutralize with saturated sodium carbonate solution, extract with ethyl acetate, separate the upper layer solution, wash with saturated saline solution until neutral, and dry over anhydrous sodium sulfate. The solvent was removed, and a colorless liquid was obtained by distillation under reduced pressure with a yield of 90%. 1 HNMR (TMS, CDCl 3 , ppm): δ1.12~1.13 (6H, t, methyl H), 1.3~1.4 (10H, m, methylene H of cyclohexane), 2.48 (4H, s, methylene H), 4.0 ~4.1 (4H, m, methylene H of ethanol)
[0059] (2) Preparation of 1,1-diethanol cycloh...
Embodiment 3
[0063] Example 3 Preparation of 1,5-diphenyl-1,5-pentanediol dibenzoate
[0064] (1) Preparation of 1,5-diphenyl-1,5-pentanediol
[0065] Add 100ml of anhydrous tetrahydrofuran to 3g of lithium aluminum hydride, and stir vigorously under ice-bath cooling. Slowly add 0.05mol 1,5-diphenyl-1,5-pentanedione dropwise, then heat to reflux for 5h. After cooling, decompose excess lithium aluminum tetrahydrogen with water, stir the extraction solution with ethyl acetate, filter, and dry over anhydrous sodium sulfate. The solvent was removed, and the white solid 1,5-diphenyl-1,5-pentanediol was obtained by column chromatography, the yield was 85%, and the mp was 64-67°C. IR spectrum at 3400cm -1 There is a strong -OH absorption peak at 1700cm -1 There is no -CO- absorption peak on the left and right, which proves that the reduction reaction is complete.
[0066] (2) Preparation of 1,5-diphenyl-1,5-pentanediol dibenzoate
[0067] Add 30ml tetrahydrofuran and 0.09mol pyridine to 0.0...
PUM
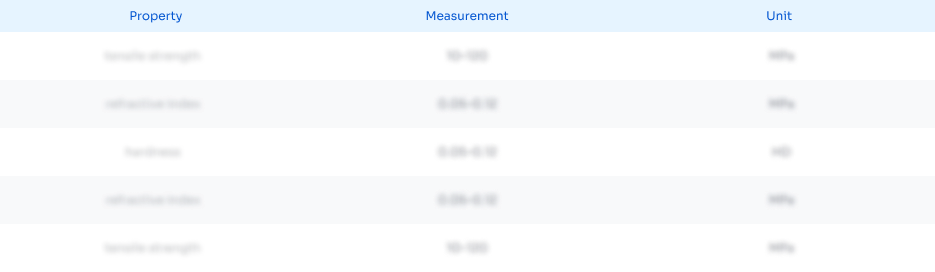
Abstract
Description
Claims
Application Information

- R&D
- Intellectual Property
- Life Sciences
- Materials
- Tech Scout
- Unparalleled Data Quality
- Higher Quality Content
- 60% Fewer Hallucinations
Browse by: Latest US Patents, China's latest patents, Technical Efficacy Thesaurus, Application Domain, Technology Topic, Popular Technical Reports.
© 2025 PatSnap. All rights reserved.Legal|Privacy policy|Modern Slavery Act Transparency Statement|Sitemap|About US| Contact US: help@patsnap.com