Ionized PVD with sequential deposition and etching
An etching and deposition mode technology, applied in the field of metallization, can solve problems such as uneven etching of substrates, cost barriers, and polluted films, and achieve the effects of excellent channel structure metallization, optimized processing pressure, and optimized ionization deposition
- Summary
- Abstract
- Description
- Claims
- Application Information
AI Technical Summary
Benefits of technology
Problems solved by technology
Method used
Image
Examples
Embodiment Construction
[0030] figure 1Denotes the deposition of a metal film 10 by iPVD in a channel structure 11 in a dielectric interlayer 13 of a semiconductor wafer 12 . As metal ions 18 are deposited on wafer 12, the metal deposit tends to thicken at the channel structure entrance, forming protruding structures 14. Likewise, the metal is deposited thicker at the bottom 15 of the trench structure 11 than at the sidewalls 16 . As the size of the channel structure decreases below 0.15 microns, but the thickness of the dielectric interlayer 13 does not decrease, the aspect ratio of the channel structure 11 will increase significantly, limiting the ability to reach the sidewall 16 of the channel structure 11. flow of metal ions14. For thinner depositions of less than 100 Å, the film deposited on the sidewalls 16 of the trench structure 11, especially for metal seed layers such as copper, tends to form agglomerated island structures. Gaps and discontinuities in the copper seed layer result in the ...
PUM
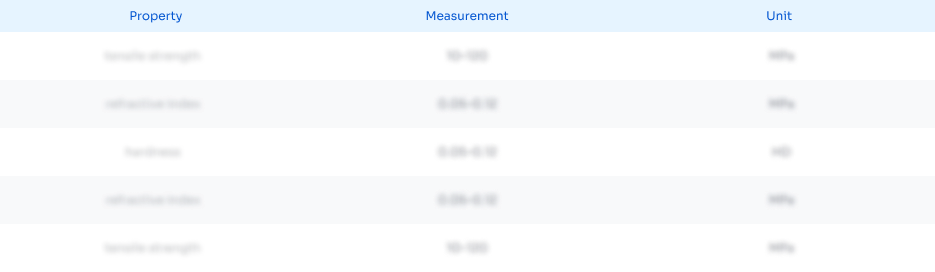
Abstract
Description
Claims
Application Information

- R&D Engineer
- R&D Manager
- IP Professional
- Industry Leading Data Capabilities
- Powerful AI technology
- Patent DNA Extraction
Browse by: Latest US Patents, China's latest patents, Technical Efficacy Thesaurus, Application Domain, Technology Topic, Popular Technical Reports.
© 2024 PatSnap. All rights reserved.Legal|Privacy policy|Modern Slavery Act Transparency Statement|Sitemap|About US| Contact US: help@patsnap.com