Method and apparatus for thixotropic molding of semisolid alloys
A molding method and semi-solid technology, applied in the field of semi-solid alloy injection molding and equipment, can solve the problems of increasing manufacturing and maintenance costs, dendrite degradation, slurry back leakage, etc., so as to reduce maintenance costs, reduce construction materials, The effect of simplifying process operations
- Summary
- Abstract
- Description
- Claims
- Application Information
AI Technical Summary
Problems solved by technology
Method used
Image
Examples
Embodiment Construction
[0034] The main difference between the injection molding method provided by the present invention and existing methods is that it does not use conventional extrusion screws or pistons. In this way, while retaining most of the characteristics of traditional injection machines, equipment and operating costs can be greatly reduced.
[0035] The method is realized by the following steps: a non-dendritic raw material rod is fed into an extrusion sleeve, and a given length of the end of the raw material rod is heated to a temperature between its solidus line and liquidus line A semi-solid slurry is produced and the solid portion of the stock rod is used to act like a disposable piston to inject the semi-solid slurry in front of it into a mold cavity.
[0036] The above steps can be used as figure 1Shown injection molding machine (10) to complete. The injection machine (10) comprises an extrusion sleeve (11) equipped with an injection nozzle (12) at the front end. The nozzle (12) ...
PUM
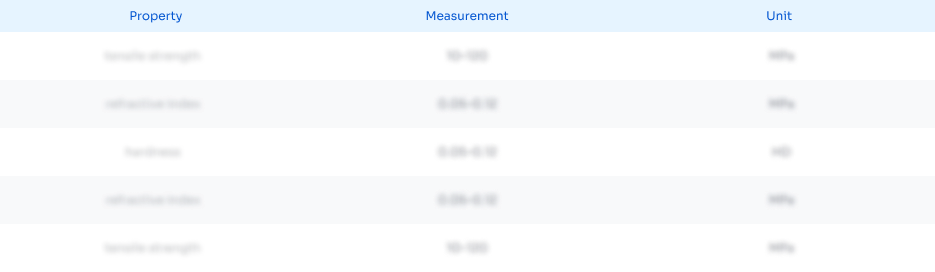
Abstract
Description
Claims
Application Information

- R&D
- Intellectual Property
- Life Sciences
- Materials
- Tech Scout
- Unparalleled Data Quality
- Higher Quality Content
- 60% Fewer Hallucinations
Browse by: Latest US Patents, China's latest patents, Technical Efficacy Thesaurus, Application Domain, Technology Topic, Popular Technical Reports.
© 2025 PatSnap. All rights reserved.Legal|Privacy policy|Modern Slavery Act Transparency Statement|Sitemap|About US| Contact US: help@patsnap.com