Wax dielectric for heating temperature control valve and its preparing method
A technology of temperature control valve and wax medium, which is applied in the field of special wax, can solve the problems of no performance, suitable temperature-sensing wax material, and no technical disclosure, etc., and achieve the effects of stable product performance, long service life, and good use effect
- Summary
- Abstract
- Description
- Claims
- Application Information
AI Technical Summary
Problems solved by technology
Method used
Image
Examples
Embodiment 1
[0020] (1) With liquid paraffin as raw material, in a distillation unit with 17 theoretical plates, at 1.33 × 10 3 Under the pressure of Pa, the fractions of 260-340°C were prepared at intervals of 5°C, and the melting points of the fractions were shown in Table 1;
[0021] (2) the above-mentioned cuts are carried out sweating and purifying with its melting point as the end point temperature, and the melting points of each purified component are as shown in Table 1;
[0022] Table 1 Vacuum distillation of each component - sweating product melting point
[0023] Distillation range °C Melting point of vacuum distillation product °C Melting point of sweating product °C
[0024] 260~265 5.0 5.3
[0025] 265~270 6.9 7.0
[0026] 270~275 9.0 9.2
[0027] 275~280 11.0 11.1
[0028] 280~285 13.0 13.3
[0029] 285~290 15.1 15.4
[0030] 290~295 17.1 17.3
[0031] 295~300 19.0 19.2
[0032] 300~305 20.9 21.1
[00...
Embodiment 2
[0045] (1) With liquid paraffin as raw material, in a distillation unit with 17 theoretical plates, at 1.33 × 10 3 Under Pa pressure, 260-300°C fractions were prepared at intervals of 10°C; under the same distillation conditions, soap wax (melting point 42.5°C) was used as raw material to prepare 300-340°C fractions, and the melting points of each fraction product were shown in Table 2. shown;
[0046] (2) the above-mentioned cuts are carried out sweating and purifying with its melting point as the end point temperature, and the melting points of each purified component are as shown in Table 2;
[0047] (3) The above-mentioned components purified by sweating are sampled in the same proportion by weight, heated and melted, and mixed uniformly;
[0048] (4) Add 5% activated clay to the above mixed components at 120° C., mix for 0.5 hours and then filter to obtain the target product.
[0049]The expansion performance curve of the heating temperature control valve made of this p...
Embodiment 3
[0062] (1) With liquid paraffin as raw material, in a distillation unit with 17 theoretical plates, at 1.33 × 10 3 Under the pressure of Pa, the fractions of 260-300°C were prepared at intervals of 20°C; under the same distillation conditions, the fractions of 300-340°C were prepared using the minus-line wax paste as the raw material. The melting points of the products of each fraction are shown in Table 3;
[0063] (2) the above-mentioned cuts are carried out sweating and purifying with its melting point as the end point temperature, and the melting points of each purified component are as shown in table 3;
[0064] (3) The above-mentioned components purified by sweating are sampled in the same proportion by weight, heated and melted, and mixed uniformly;
[0065] (4) Add 4% activated clay to the above mixed components at 130° C., mix for 0.5 hours and then filter to obtain the target product.
[0066] The expansion performance curve of the heating temperature control valve ...
PUM
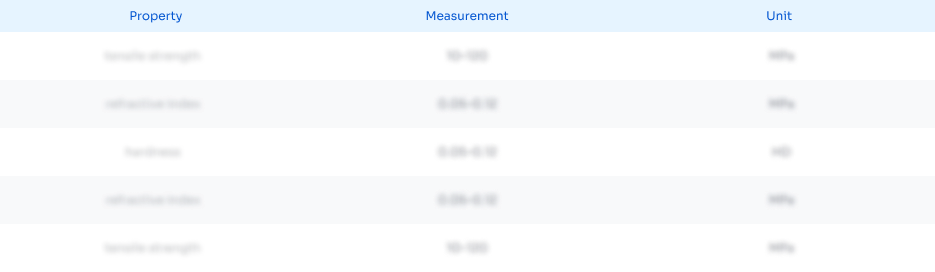
Abstract
Description
Claims
Application Information

- R&D
- Intellectual Property
- Life Sciences
- Materials
- Tech Scout
- Unparalleled Data Quality
- Higher Quality Content
- 60% Fewer Hallucinations
Browse by: Latest US Patents, China's latest patents, Technical Efficacy Thesaurus, Application Domain, Technology Topic, Popular Technical Reports.
© 2025 PatSnap. All rights reserved.Legal|Privacy policy|Modern Slavery Act Transparency Statement|Sitemap|About US| Contact US: help@patsnap.com