High temperature high pressure jet dyeing process and apparatus for color fabrics
A high-pressure jetting and textile technology, applied in the field of printing and dyeing, can solve the problems of large waste of dyes, energy waste, waste of dyes, etc., and achieve the effect of shortening the dyeing process and time, reducing printing and dyeing costs, and high utilization of dyes
- Summary
- Abstract
- Description
- Claims
- Application Information
AI Technical Summary
Problems solved by technology
Method used
Image
Examples
Embodiment 1
[0023] A semi-new bright blue sweater weighing 500 grams was dyed bright green.
[0024] The dye weight of the above-mentioned brilliant blue sweater according to the calculation formula is:
[0025] 500×1%=5 grams
[0026] If 50% of the color is removed, the weight of the remaining dye is:
[0027] 5 x 50% = 2.5 grams
[0028] According to the principle of color matching, bright blue and bright yellow are combined into bright green, and the bright yellow dye is taken according to the medium color ratio;
[0029] Dye: Acid Bright Yellow 2G 5g
[0030] Acid Brilliant Blue 2.5g
[0031] Dyeing aid: Glacial acetic acid HAC 50ml
[0032] Leveling Agent O 10ml
[0033] Diffuser NNO 10ml
[0034] Penetrant JFC 10ml
[0035] Bath ratio: 1:10
[0036] First put the sweater in the steam dyeing room for 10 minutes under normal pressure, then take it out and wait for spray dyeing. Then dissolve the weighed dye with water at 20-40°C to make a dye so...
Embodiment 2
[0038] A pair of dark gray jeans, 500 grams, dyed into navy blue.
[0039] According to the calculation, it can be obtained that:
[0040] Dye: Direct Fast Blue B2RL 10g
[0041] Dyeing aid: NaCl 200g
[0042] Soda ash 10 grams
[0043] Silky Soap 5ml
[0044] Yuanming powder 5 grams
[0045] Diffuser NNO 10ml
[0046] Penetrant JFC 10ml
[0047] Liquor ratio: 1:8 Clothes steaming bath is the same as that of dissolving dye as in Example 1. Adjust the dyeing solution according to the liquor ratio of 1:8. After dissolving various auxiliaries, pour them into the dye vat, stir well, cover and heat , the rest of the process is the same as
[0048] Example 1 is the same.
Embodiment 3
[0050] A pair of dark gray jeans weighs about 500 grams, faded by 30%, and want to return to the original dark gray,
[0051] According to the calculation, the dye weight of the standard dark gray jeans is
[0052] 500 2% = 10 grams
[0053] fade color dye heavy
[0054] 10 grams 30% = 3 grams to take dye: direct ash D 3 grams
[0055] Auxiliary: 50 grams of table salt (NaCl)
[0056] Diffuser NNO 10ml
[0057] Leveling Agent O 10ml
[0058] Penetrant JFC 10ml Bath ratio: 1:10 Other processes are the same as in Example 1.
PUM
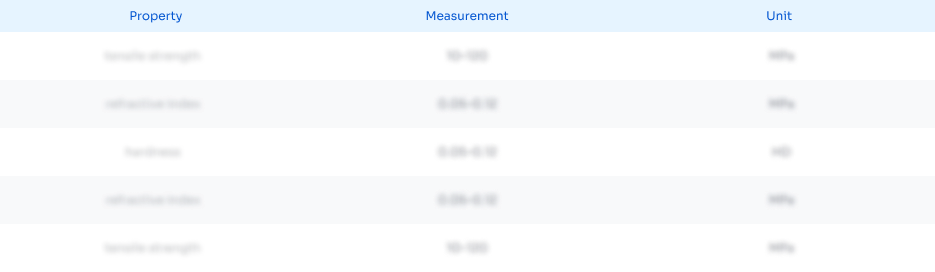
Abstract
Description
Claims
Application Information

- R&D
- Intellectual Property
- Life Sciences
- Materials
- Tech Scout
- Unparalleled Data Quality
- Higher Quality Content
- 60% Fewer Hallucinations
Browse by: Latest US Patents, China's latest patents, Technical Efficacy Thesaurus, Application Domain, Technology Topic, Popular Technical Reports.
© 2025 PatSnap. All rights reserved.Legal|Privacy policy|Modern Slavery Act Transparency Statement|Sitemap|About US| Contact US: help@patsnap.com