Method for making composite membrane for separation of polymer fluid
A manufacturing method, a fluid separation technology, applied in the direction of semi-permeable membrane separation, chemical instruments and methods, membrane technology, etc., can solve problems such as difficult guarantees, and achieve completely unblocked pore channels, high permeation flux, and high intrinsic permeability Effect
- Summary
- Abstract
- Description
- Claims
- Application Information
AI Technical Summary
Problems solved by technology
Method used
Image
Examples
Embodiment 1
[0020] A circular support layer microporous membrane with a diameter of 200 mm was produced by solvent evaporation method. The polymer material used was polysulfone (PS), the micropore size was 0.6 micron, the porosity was 60%, and the microporous film thickness was 150 micron. Use the solvent glycerin to filter through this microporous membrane to make the pores saturated with glycerin, and carefully remove the glycerin on the surface of the membrane. Polyvinyl alcohol (PVA) and corresponding cross-linking agents, additives and compounding agents are dissolved in solvent water to prepare a film-forming solution for the active skin layer of polyvinyl alcohol. The concentration of polyvinyl alcohol is 5% (W / W). Coat the polyvinyl alcohol membrane-making solution on the polysulfone support membrane whose pores are saturated with glycerin, and then place it at a temperature of 60°C to solidify the polyvinyl alcohol to form an active skin layer, and then place the membrane at a tem...
Embodiment 2
[0022] Adopt the solvent volatilization method to make a circular support layer microporous membrane with a diameter of 200 mm. The material used is polyacrylonitrile (PAN). is 150 microns. Use solvent glycerin to filter through this microporous membrane to make the pores saturated with glycerin, and carefully remove the glycerin on the surface of the membrane. Polyvinyl alcohol (PVA) and corresponding cross-linking agents, additives and compounding agents are dissolved in solvent water, the concentration of polyvinyl alcohol is 2% (W / W), and the film-forming solution of the active skin layer of polyvinyl alcohol is prepared. Coat the film-making solution on the microporous polyvinyl nitrile support membrane saturated with glycerol, place it at a temperature of 60°C to solidify the polyvinyl alcohol to form an active skin layer, and then place the film at a temperature of 100°C and 10kPa Treat under vacuum for 2 hours to obtain a dry composite film. The SEM photograph of the...
Embodiment 3
[0024] The polysulfone (PS) microporous hollow fiber membrane is made by the L-S phase inversion method, the outer diameter of the fiber tube is 500 microns, the inner diameter is 250 microns, and the pore diameter is 0.1 microns. Immerse the fiber tube in solvent water to saturate the pores with water. Polydimethylsiloxane (PDMS) and corresponding crosslinking agents, catalysts and additives were dissolved in solvent benzene, and the concentration of polydimethylsiloxane (PDMS) was 10% (W / W). Seal both ends of the fiber tube, then immerse it in polydimethylsiloxane film-making solution for 1-2 mm, take it out to let the benzene volatilize naturally, and then place it at a temperature of 100 ° C and treat it under a vacuum of 10 kPa for 3 hours to form a dry hollow fiber composite membrane. The SEM photograph of the composite film shows that the thickness of the polydimethylsiloxane (PDMS) composite layer is 2 microns. When used for air separation, O 2 / N 2 The separation ...
PUM
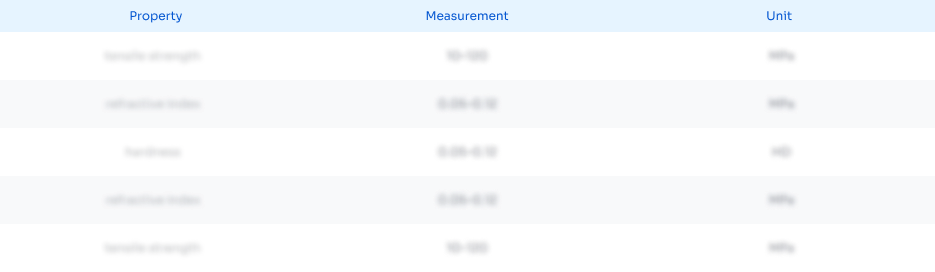
Abstract
Description
Claims
Application Information

- R&D
- Intellectual Property
- Life Sciences
- Materials
- Tech Scout
- Unparalleled Data Quality
- Higher Quality Content
- 60% Fewer Hallucinations
Browse by: Latest US Patents, China's latest patents, Technical Efficacy Thesaurus, Application Domain, Technology Topic, Popular Technical Reports.
© 2025 PatSnap. All rights reserved.Legal|Privacy policy|Modern Slavery Act Transparency Statement|Sitemap|About US| Contact US: help@patsnap.com