System for optimum SCR operation for controlling exhaust temp of flue
A technology of gas temperature and flue, which is applied in the direction of flue gas purification components, steam boiler components, separation methods, etc., can solve the problems of serious changes in gas flow and temperature, etc.
- Summary
- Abstract
- Description
- Claims
- Application Information
AI Technical Summary
Problems solved by technology
Method used
Image
Examples
Embodiment Construction
[0014] Referring to Figures 1 and 2, the present invention uses different methods to obtain the TPP boiler exhaust temperature. In normal boiler applications, one side of the economizer's water flow is used to cool the flue gas flowing over surfaces mounted inside the boiler. Here, the boiler recirculation system (10) is modified to get a near-saturated higher temperature water flow input to the inlet (16) of the economizer (18) from the downcomer (12) connected by the bypass pipe (14). This inlet (16) is a T-shaped inlet with the other input of the T providing the normal feed water flow from the line (20). The water flow through the pipeline (14) is provided by the pump (22) being monitored, and flow F and pressure P sensors are installed on both sides of the pump (22). Economizer (18) bypass line (24) is provided as shown in dotted line in Figure 1 to allow the downpipe ( 12) Saturated water is recirculated from the cylinder (26) back to the bypass pipe (24).
[0015] spe...
PUM
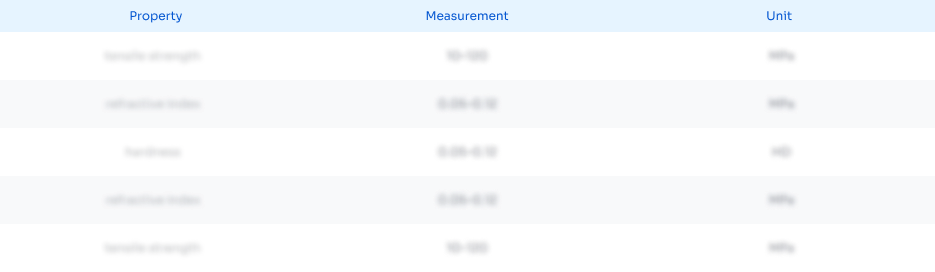
Abstract
Description
Claims
Application Information

- Generate Ideas
- Intellectual Property
- Life Sciences
- Materials
- Tech Scout
- Unparalleled Data Quality
- Higher Quality Content
- 60% Fewer Hallucinations
Browse by: Latest US Patents, China's latest patents, Technical Efficacy Thesaurus, Application Domain, Technology Topic, Popular Technical Reports.
© 2025 PatSnap. All rights reserved.Legal|Privacy policy|Modern Slavery Act Transparency Statement|Sitemap|About US| Contact US: help@patsnap.com