Method for synthesizing Al203/TiAl composite material
A synthesis method and technology of composite materials, applied in the field of preparation of intermetallic compounds/ceramic composite materials, can solve the problems of difficult ceramic phase particle distribution, material performance barriers, difficult to eliminate pores, etc., and achieve uniform, dense and adjustable structure Great, low-cost effect
- Summary
- Abstract
- Description
- Claims
- Application Information
AI Technical Summary
Problems solved by technology
Method used
Image
Examples
Embodiment 1
[0009] Embodiment 1: at first 64% Ti and 36% Al are made mixture by mass percentage; Add the sodium stearate dispersant of mixture quality 0.5% in the mixture, adopt dry ball milling, make its mechanical alloying, wherein , the rotational speed of the planetary ball mill is 700 rev / min, the mass ratio of material to ball is 1:10, ball milling for 20 hours, and the amorphous fine powder whose main crystal phase is TiAlO is formed; the alloyed amorphous powder is heated at 70°C Dry under high temperature for 5 hours; put the dried powder into a graphite grinding tool, and sinter it under argon at 1200°C and a pressure of 20MPa for 1.5 hours.
Embodiment 2
[0010] Embodiment 2: at first by mass percentage the Al of 56% and the TiO of 44% 2 Make mixture; Add the sodium stearate dispersant of mixture quality 0.2% in mixture, adopt dry ball milling, make its mechanical alloying, wherein, the rotating speed of planetary ball mill is 800 rev / mins, and material ball mass ratio is 1 : 10, ball milled for 24 hours to form an amorphous fine powder whose main crystal phase is TiAlO; the alloyed amorphous powder was dried at 78°C for 4.2 hours; the dried powder was packed into a graphite grinding tool, Under the condition of argon, it can be hot-pressed and sintered at 1000°C and a pressure of 10 MPa for 2.5 hours.
Embodiment 3
[0011] Embodiment 3: first by mass percentage 25% Ti, 40% Al and 35% TiO 2 Make mixture; Add the sodium stearate dispersant of mixture quality 0.4% in mixture, adopt dry method ball mill, make its mechanical alloying, wherein, the rotating speed of planetary ball mill is 780 rev / mins, and material ball mass ratio is 1 : 10, ball milled for 23 hours to form an amorphous fine powder whose main crystal phase is TiAlO; the alloyed amorphous powder was dried at 72°C for 4 hours; the dried powder was packed into a graphite grinding tool, and the Under the condition of argon, it can be hot-pressed and sintered at 1150 ° C and 35 MPa for 1.8 hours.
PUM
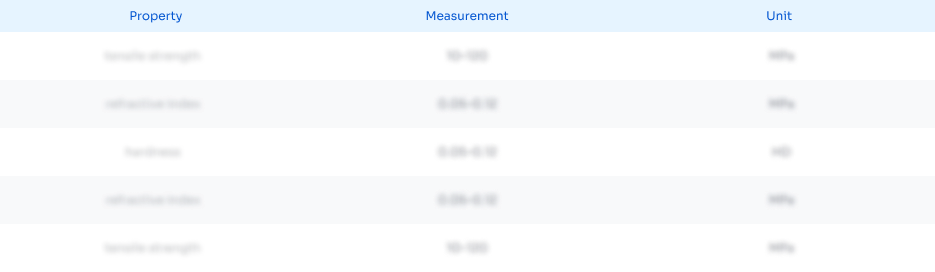
Abstract
Description
Claims
Application Information

- R&D
- Intellectual Property
- Life Sciences
- Materials
- Tech Scout
- Unparalleled Data Quality
- Higher Quality Content
- 60% Fewer Hallucinations
Browse by: Latest US Patents, China's latest patents, Technical Efficacy Thesaurus, Application Domain, Technology Topic, Popular Technical Reports.
© 2025 PatSnap. All rights reserved.Legal|Privacy policy|Modern Slavery Act Transparency Statement|Sitemap|About US| Contact US: help@patsnap.com