Configuration of coolable turbine blade
A technology for turbine blades and cooling fluids, applied in the direction of blade support elements, engine functions, mechanical equipment, etc., can solve problems such as geometric structure restrictions, trailing edge overheating, etc., and achieve a soft transition effect
- Summary
- Abstract
- Description
- Claims
- Application Information
AI Technical Summary
Problems solved by technology
Method used
Image
Examples
Embodiment Construction
[0029] The turbine blades 1 are surrounded by a working fluid 3 (only a part of which is shown as an example in FIG. 1 ) in the outflow direction 2 , thereby producing work and driving the turbine. Turbine blade 1 is cooled by fluid 31 (the cooling fluid is in figure 2 , likewise only partly shown as an example), flow along the flow channels 4 , 5 , 6 . This cools the turbine blade 1 . The cooling fluid 31 can be (cooling) air, for example.
[0030]The turbine blade 1 has a blade root 10 which is inserted into a corresponding groove on the turbine disk (not shown in the figure) and fixed there. The inflow holes 7, 8, 9 are shown in alignment with corresponding holes in the turbine wheel. The cooling fluid 31 is fed into the flow channels 4 , 5 , 6 through them.
[0031] The flow channels 4 , 5 , 6 are between the inflow holes 7 , 8 , 9 at the radially inner blade root 10 and the radially outer outlet holes 11 , 12 , 13 opposite the blade root 10 extend. This extension ha...
PUM
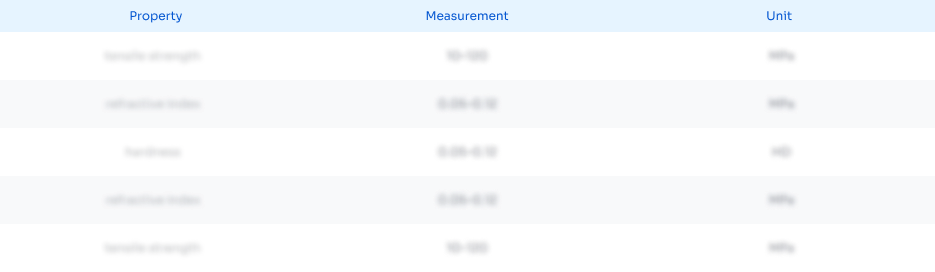
Abstract
Description
Claims
Application Information

- R&D
- Intellectual Property
- Life Sciences
- Materials
- Tech Scout
- Unparalleled Data Quality
- Higher Quality Content
- 60% Fewer Hallucinations
Browse by: Latest US Patents, China's latest patents, Technical Efficacy Thesaurus, Application Domain, Technology Topic, Popular Technical Reports.
© 2025 PatSnap. All rights reserved.Legal|Privacy policy|Modern Slavery Act Transparency Statement|Sitemap|About US| Contact US: help@patsnap.com