Combine
A combine harvester and vertical axis technology, which is applied in the direction of harvesters, cutters, agricultural machinery and implements, etc., can solve the problems of not being able to easily support the structure and manufacturing costs, the disorder of the conveying posture, and the widening of the setting width, so as to eliminate the The rod contacts the branch box, reducing the conveying disturbance and ensuring the effect of compactness
- Summary
- Abstract
- Description
- Claims
- Application Information
AI Technical Summary
Problems solved by technology
Method used
Image
Examples
Embodiment Construction
[0028] Embodiments of the present invention will be described in detail below with reference to the drawings. figure 1 For the overall left view, figure 2 for its floor plan. The symbol 1 in the figure is a crawler frame with a pair of walking crawlers 2 installed, the symbol 3 is a machine set on the upper side of the crawler frame 1, and the symbol 4 is a feed chain 5 stretched on the left side and a threshing drum 6 and a processing cylinder inside. The threshing part of 7, symbol 8 is the cutting part that has cutting knife 9 and straw conveying mechanism 10 etc., and symbol 11 is the hydraulic cylinder that makes cutting part 8 lift by cutting frame 12, and symbol 13 is facing the straw discharge chain 14 terminal straw discharge cutter, symbol 15 is the grain case that the grain from the threshing section 4 is carried in by raising the grain cylinder 16, and the symbol 17 is the grain receiving platform that the grain of the above-mentioned case 15 is carried out to th...
PUM
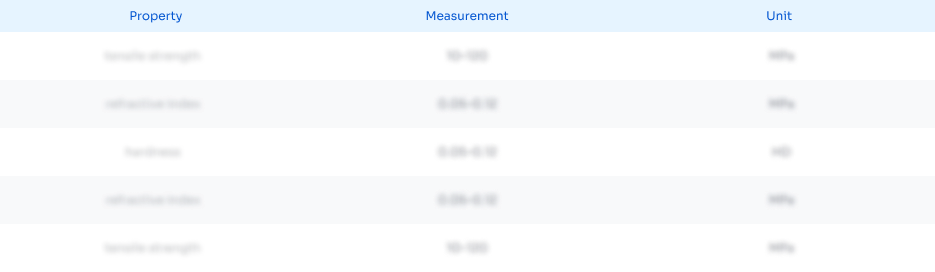
Abstract
Description
Claims
Application Information

- R&D
- Intellectual Property
- Life Sciences
- Materials
- Tech Scout
- Unparalleled Data Quality
- Higher Quality Content
- 60% Fewer Hallucinations
Browse by: Latest US Patents, China's latest patents, Technical Efficacy Thesaurus, Application Domain, Technology Topic, Popular Technical Reports.
© 2025 PatSnap. All rights reserved.Legal|Privacy policy|Modern Slavery Act Transparency Statement|Sitemap|About US| Contact US: help@patsnap.com