Design method for improving PCB bow
A design method and bowing technology, applied in printed circuits, electrical components, printed circuit manufacturing, etc., can solve problems such as PCB bowing, and achieve the effects of reducing internal stress, uniform copper distribution, and consistent heating speed
- Summary
- Abstract
- Description
- Claims
- Application Information
AI Technical Summary
Problems solved by technology
Method used
Image
Examples
Embodiment
[0029] A design method for improving PCB bowing shown in this embodiment includes the following steps in turn:
[0030] a. The copper clad core board is cut out according to the size of the panel of 520mm×620mm, with the long side as the warp direction and the short side as the weft direction.
[0031] b. If figure 1 As shown in the figure, the copper clad core board is typeset to design a number of circuit board units (ie SET boards) on the copper clad core board according to the typesetting requirements, and each circuit board unit includes at least one unit board (ie PCS) ; Wherein, at least two columns of first circuit board units 2 whose length direction is parallel to the meridian direction of the copper clad core board are arranged on the copper clad core board 1, and at least one column of length is set between the first circuit board units 2 of two adjacent columns. The second circuit board unit 3 whose direction is parallel to the latitudinal direction of the CCL, t...
PUM
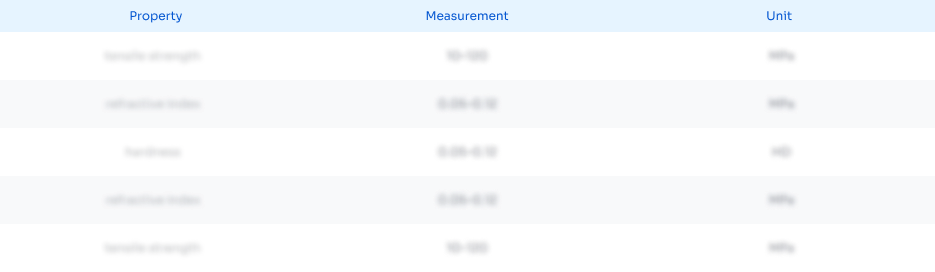
Abstract
Description
Claims
Application Information

- R&D Engineer
- R&D Manager
- IP Professional
- Industry Leading Data Capabilities
- Powerful AI technology
- Patent DNA Extraction
Browse by: Latest US Patents, China's latest patents, Technical Efficacy Thesaurus, Application Domain, Technology Topic, Popular Technical Reports.
© 2024 PatSnap. All rights reserved.Legal|Privacy policy|Modern Slavery Act Transparency Statement|Sitemap|About US| Contact US: help@patsnap.com