Method for evaluating low-speed impact damage residual strength of winding composite material structure
A technology for winding composite materials and low-velocity impact damage, which is applied to instruments, design optimization/simulation, calculation, etc., to achieve simple and effective analysis methods and avoid deviations in calculation results
- Summary
- Abstract
- Description
- Claims
- Application Information
AI Technical Summary
Problems solved by technology
Method used
Image
Examples
Embodiment Construction
[0025] The technical solutions in the embodiments of the present invention will be described clearly and completely below. Obviously, the described embodiments are only a part of the embodiments of the present invention, rather than all the embodiments. Based on the embodiments of the present invention, all other embodiments obtained by those of ordinary skill in the art without creative efforts shall fall within the protection scope of the present invention.
[0026] First of all, it should be noted that, in the implementation process of the present invention, the application of multiple software function modules will be involved. The applicant believes that after carefully reading the application documents and accurately understanding the realization principle and purpose of the present invention, those skilled in the art can fully implement the present invention by using the software programming skills mastered by them.
[0027] Step 1: Simulation calculation of low-speed i...
PUM
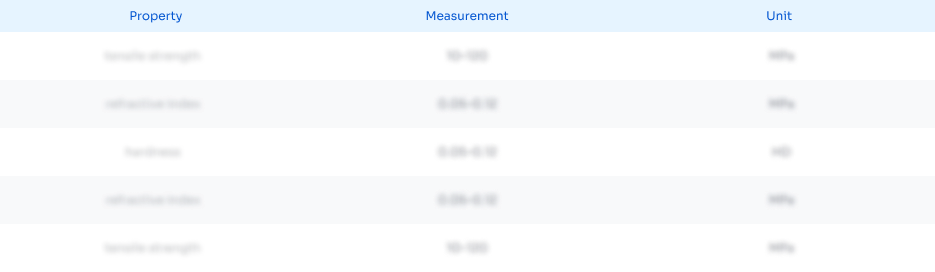
Abstract
Description
Claims
Application Information

- R&D Engineer
- R&D Manager
- IP Professional
- Industry Leading Data Capabilities
- Powerful AI technology
- Patent DNA Extraction
Browse by: Latest US Patents, China's latest patents, Technical Efficacy Thesaurus, Application Domain, Technology Topic, Popular Technical Reports.
© 2024 PatSnap. All rights reserved.Legal|Privacy policy|Modern Slavery Act Transparency Statement|Sitemap|About US| Contact US: help@patsnap.com