Cable-free three-degree-of-freedom joint module and bionic leg and foot structure
A technology of degrees of freedom and joints, applied in the field of bionic robots, can solve problems such as cable breakage and poor contact, and achieve the effects of high reliability, easy disassembly and maintenance, large movement space and maneuverability
- Summary
- Abstract
- Description
- Claims
- Application Information
AI Technical Summary
Problems solved by technology
Method used
Image
Examples
Embodiment Construction
[0029] In order to make the purpose, content and advantages of the present invention clearer, the specific embodiments of the present invention will be described in further detail below.
[0030] A cable-free three-degree-of-freedom joint module proposed by the present invention includes a lateral expansion joint 101, a front swing joint 102, a knee joint 103, and a knee joint installation flange 104;
[0031] The knee joint and the front swing joint are arranged in the same direction, the rotation axis of the lateral joint 101 is perpendicular to the axis of the front swing knee joint, the front swing joint is a hollow structure, and the power line and control line of the knee joint module pass through the front swing motor hollow shaft. lead out, so as to realize the cable-free design of the knee joint module.
[0032] The tail end of the knee joint is fixedly connected to the output end of the front swing joint, the motor of the front swing joint is fixedly connected to the...
PUM
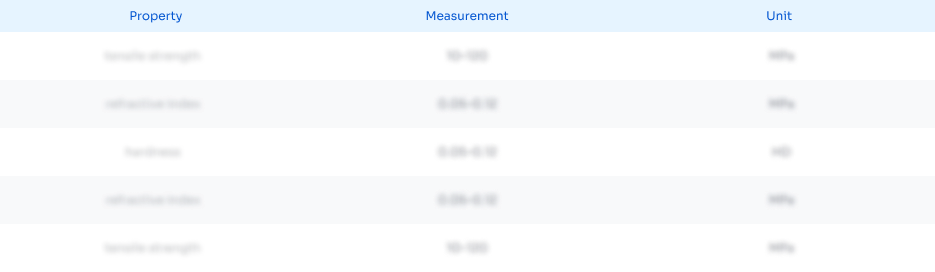
Abstract
Description
Claims
Application Information

- R&D Engineer
- R&D Manager
- IP Professional
- Industry Leading Data Capabilities
- Powerful AI technology
- Patent DNA Extraction
Browse by: Latest US Patents, China's latest patents, Technical Efficacy Thesaurus, Application Domain, Technology Topic, Popular Technical Reports.
© 2024 PatSnap. All rights reserved.Legal|Privacy policy|Modern Slavery Act Transparency Statement|Sitemap|About US| Contact US: help@patsnap.com