Aluminum alloy auxiliary frame
A subframe and aluminum alloy technology, which is applied to vehicle parts, substructure, transportation and packaging, etc., can solve the problems of many welding processes, difficult control of dimensional accuracy, and abnormal noise of bushing installation, so as to reduce its own quality, Save the cost of sand core and manufacturing process, and ensure the effect of metallurgical quality
- Summary
- Abstract
- Description
- Claims
- Application Information
AI Technical Summary
Problems solved by technology
Method used
Image
Examples
Embodiment Construction
[0019] like Figure 1 to Figure 2 As shown, an aluminum alloy sub-frame includes: a sub-frame body 1, the sub-frame body 1 is made of high-performance aluminum alloy material by integral molding, and a plurality of reinforcing ribs 2 are arranged on the sub-frame body 1 , the reinforcing ribs 2 are radially distributed on the sub-frame body 1 , and a plurality of weight reduction holes 3 are arranged on the sub-frame body 1 . The upper left corner of the sub-frame body 1 is provided with a left front body mounting bracket 11, the upper right corner is provided with a right front body mounting bracket 12, the lower left corner is provided with a left rear body mounting bracket 13, and the lower right corner is provided with a right rear body mounting bracket 14; Among them, the left front body mounting bracket 11 , the right front body mounting bracket 12 , the left rear body mounting bracket 13 , and the right rear body mounting bracket 14 are precast holes with a design of Ф6...
PUM
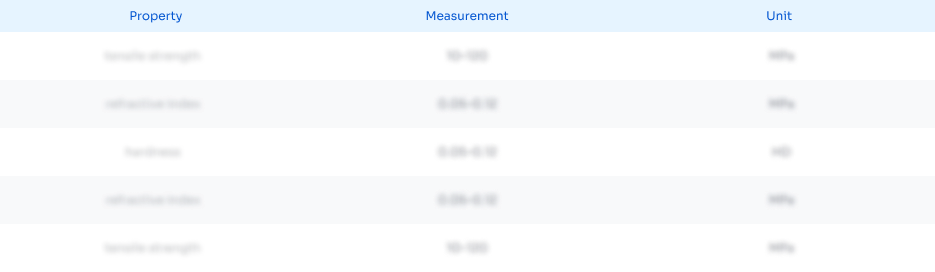
Abstract
Description
Claims
Application Information

- Generate Ideas
- Intellectual Property
- Life Sciences
- Materials
- Tech Scout
- Unparalleled Data Quality
- Higher Quality Content
- 60% Fewer Hallucinations
Browse by: Latest US Patents, China's latest patents, Technical Efficacy Thesaurus, Application Domain, Technology Topic, Popular Technical Reports.
© 2025 PatSnap. All rights reserved.Legal|Privacy policy|Modern Slavery Act Transparency Statement|Sitemap|About US| Contact US: help@patsnap.com