Efficient injection mold
A technology of injection molds and molds, which is applied in the field of high-efficiency injection molds, can solve problems such as time-consuming, and achieve the effects of safe demoulding, high efficiency, and reduced chances of breaking
- Summary
- Abstract
- Description
- Claims
- Application Information
AI Technical Summary
Problems solved by technology
Method used
Image
Examples
Embodiment approach
[0054] As an embodiment of the present invention, the airbag 9 is filled with lubricating powder; during operation, when the airbag 9 is pressed and extruded, the airbag 9 will bring out the lubricating powder inside, and the brought out lubricating powder falls in a parabolic shape into the flexible film 22, thereby reducing the friction between the flexible film 22 and the product, so that the product can slide into the collection box from the gap between the flexible films 22 more smoothly, preventing the product from being carried on the flexible film 22 all the time. accumulation occurs.
[0055] As an embodiment of the present invention, a vacuum cavity 16 or a thermal insulation cavity 17 is provided between the two injection cavities 11 in the mold 1; the thermal insulation cavity 17 is filled with thermal insulation materials, such as foamed polyurethane ; When working, the heat of the two injection cavities 11 will not be offset by vacuum insulation or heat insulatio...
PUM
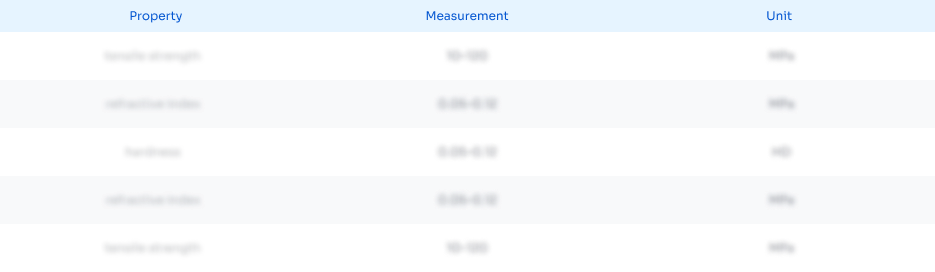
Abstract
Description
Claims
Application Information

- R&D
- Intellectual Property
- Life Sciences
- Materials
- Tech Scout
- Unparalleled Data Quality
- Higher Quality Content
- 60% Fewer Hallucinations
Browse by: Latest US Patents, China's latest patents, Technical Efficacy Thesaurus, Application Domain, Technology Topic, Popular Technical Reports.
© 2025 PatSnap. All rights reserved.Legal|Privacy policy|Modern Slavery Act Transparency Statement|Sitemap|About US| Contact US: help@patsnap.com