Automatic oiling device for bearing machining
A bearing processing and automatic technology, which is applied in the field of bearing processing, can solve the problems of unfavorable packaging operation due to oil film thickness, complicated oil film forming steps, and high labor intensity of workers, so as to improve the excessive amount of oil, reduce the cost of materials, and avoid The effect of spraying dead angle
- Summary
- Abstract
- Description
- Claims
- Application Information
AI Technical Summary
Problems solved by technology
Method used
Image
Examples
Embodiment Construction
[0031] In order to make the objectives, technical solutions and advantages of the present invention clearer, the present invention will be further described in detail below with reference to the specific embodiments and the accompanying drawings. It should be noted that the embodiments of the present invention and the features in the embodiments may be combined with each other under the condition of no conflict.
[0032] The following describes an automatic oiling device for bearing processing provided by some embodiments of the present invention with reference to the accompanying drawings.
[0033] combine Figure 1-Figure 7 As shown, an automatic oiling device for bearing processing provided by the present invention includes: a spraying frame assembly 100, a conveying frame 200, a material tray 300 and an oil film forming assembly 400, the inner side of the conveying frame 200 is fixedly installed with a lifting platform 210, The spraying rack assembly 100 and the conveying...
PUM
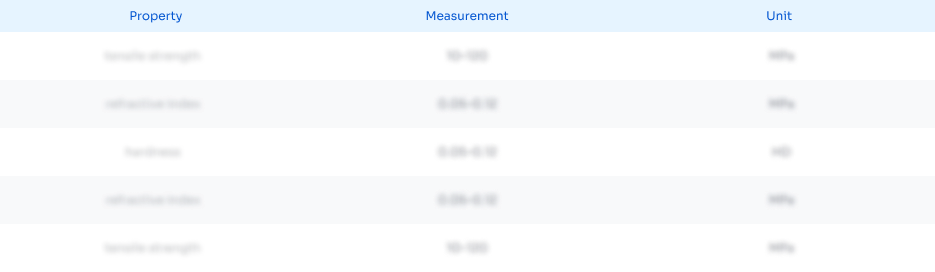
Abstract
Description
Claims
Application Information

- R&D Engineer
- R&D Manager
- IP Professional
- Industry Leading Data Capabilities
- Powerful AI technology
- Patent DNA Extraction
Browse by: Latest US Patents, China's latest patents, Technical Efficacy Thesaurus, Application Domain, Technology Topic, Popular Technical Reports.
© 2024 PatSnap. All rights reserved.Legal|Privacy policy|Modern Slavery Act Transparency Statement|Sitemap|About US| Contact US: help@patsnap.com