Production equipment and process of waterborne polyurethane foaming velvet-feeling silk-feeling synthetic leather
A technology of water-based polyurethane and production equipment, which is applied in chemical/physical/physicochemical processes, cleaning methods and utensils, chemical instruments and methods, etc., and can solve problems such as unfavorable post-cleaning of reactors, affecting hand feeling, and insufficient wear fastness
- Summary
- Abstract
- Description
- Claims
- Application Information
AI Technical Summary
Problems solved by technology
Method used
Image
Examples
Embodiment Construction
[0030] In order to make the technical means, creative features, achievement goals and effects realized by the present invention easy to understand, the present invention will be further described below with reference to the specific embodiments.
[0031] like Figure 1-Figure 8 As shown, the production equipment and process of a water-based polyurethane foamed velvet-sensing synthetic leather provided by the present invention comprises a kettle body 1, a plurality of supporting legs 2 are arranged on the bottom wall of the kettle body 1, and a top of the kettle body 1 is provided with a plurality of supporting legs 2. The side wall body is provided with a feeding pipe 3, the top of the kettle body 1 is provided with a pressure gauge 4 on the wall body located at the front end of the feeding pipe 3, and the wall body at the central position of the top of the kettle body 1 is provided with a machine base 5, the machine base 5. A first motor 6 is arranged on the top wall. The fir...
PUM
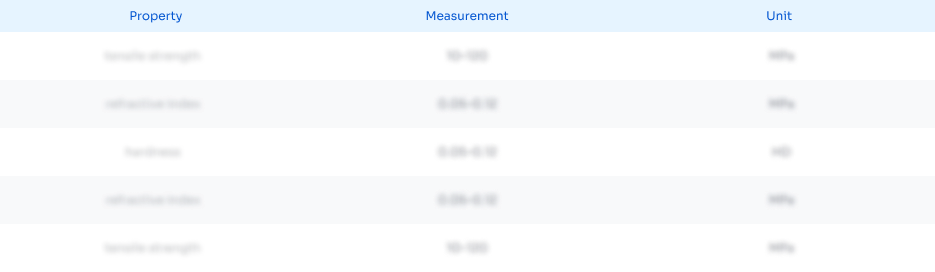
Abstract
Description
Claims
Application Information

- Generate Ideas
- Intellectual Property
- Life Sciences
- Materials
- Tech Scout
- Unparalleled Data Quality
- Higher Quality Content
- 60% Fewer Hallucinations
Browse by: Latest US Patents, China's latest patents, Technical Efficacy Thesaurus, Application Domain, Technology Topic, Popular Technical Reports.
© 2025 PatSnap. All rights reserved.Legal|Privacy policy|Modern Slavery Act Transparency Statement|Sitemap|About US| Contact US: help@patsnap.com