Polymer composite membrane for in-situ growth of MOF (Metal Organic Framework) middle layer in low-temperature water phase as well as preparation and application
A polymer and intermediate layer technology, applied in the field of membrane separation, can solve problems such as organic solvent environmental pollution, affecting the performance of selective layer composite membranes, etc., to achieve the effects of promoting absorption, improving surface morphology and properties, and enhancing binding force
- Summary
- Abstract
- Description
- Claims
- Application Information
AI Technical Summary
Problems solved by technology
Method used
Image
Examples
preparation example Construction
[0035] The invention provides a polymer composite membrane with a low-temperature water-phase in-situ growth MOF intermediate layer and its preparation method and application, mainly comprising the following steps:
[0036] (1) MOF intermediate layer grown on the surface of the polymer support layer
[0037] Put the polymer support layer in 1.0-2.0M NaOH solution for alkali treatment for 15-60 minutes, then soak in deionized water to remove the adsorbed alkali solution; then soak the alkali-treated polymer support layer in the water phase MOF growth After growing in the solution for 0.5-12 hours at 20-60°C, take it out, wash away the residual solution adsorbed on the surface and inside of the support layer with deionized water, and obtain a polymer support layer with an MOF intermediate layer after drying;
[0038] (2) Preparation of chitosan composite membrane with MOF intermediate layer
[0039] The polymer support layer with the MOF intermediate layer prepared in step (1) ...
Embodiment 1
[0060] Embodiment 1 is a polymer composite membrane based on chitosan, and the support layer of the composite membrane is a polyacrylonitrile hollow fiber membrane. The preparation process of the composite membrane includes the following steps :
[0061] (1) Prepare an aqueous NaOH solution with a molar concentration of 2M, heat it to 50° C., put it into a polyacrylonitrile support layer, and treat it with alkali for 30 minutes.
[0062] (2) Add 1.75 g of zirconium chloride, 10 mL of formic acid and 0.9 g of fumaric acid in sequence to 200 mL of deionized water, stir and dissolve to obtain a MOF growth solution. Heating to 30°C, putting the alkali-treated polyacrylonitrile support layer in, and growing in-situ in the low-temperature water phase for 12 hours, to prepare a hollow fiber support layer with an MOF middle layer.
[0063] (3) Prepare a chitosan-acetic acid-water solution with a mass fraction of 1 / 10 / 89 wt%, and fully stir until completely dissolved. The two ends ...
Embodiment 2
[0065] The experimental operation is the same as in Example 1, except that in step (3), the chitosan reaction time is 3 minutes.
PUM
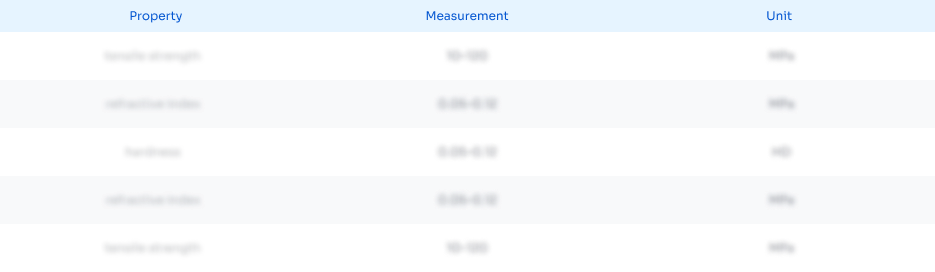
Abstract
Description
Claims
Application Information

- R&D Engineer
- R&D Manager
- IP Professional
- Industry Leading Data Capabilities
- Powerful AI technology
- Patent DNA Extraction
Browse by: Latest US Patents, China's latest patents, Technical Efficacy Thesaurus, Application Domain, Technology Topic, Popular Technical Reports.
© 2024 PatSnap. All rights reserved.Legal|Privacy policy|Modern Slavery Act Transparency Statement|Sitemap|About US| Contact US: help@patsnap.com