Hybrid energy feedback electromagnetic damper
An electromagnetic damper, a hybrid technology, applied in the direction of shock absorbers, shock absorbers, gas-hydraulic shock absorbers, etc., can solve the problems of small damping force adjustment range, small damping force maximum value, complex structure, etc., to achieve structural The assembly is simple, the maximum damping force value is increased, and the volume is small
- Summary
- Abstract
- Description
- Claims
- Application Information
AI Technical Summary
Problems solved by technology
Method used
Image
Examples
Embodiment 1
[0034] like Figure 1-6 As shown, the hybrid energy-feeding electromagnetic damper includes a piston rod 1, an upper end cover 3, a cylinder body 4, a coil 5, and a piston head 10;
[0035] The cylinder body 4 is connected to the upper end cover 3, and the inner space of the cylinder body 4 is filled with magnetorheological fluid 14; the front end of the piston rod 1 enters the cylinder body 4 through the piston rod hole in the middle of the upper end cover 3, and can be The piston rod hole slides; the piston rod 1 is connected with the piston head 10;
[0036] The inner circular surface of the cylinder body 4 is provided with an annular outer yoke 15, and the outer yoke 15 is provided with a coil groove, and the coil 5 is arranged in the coil groove and sealed by a magnetically conductive material;
[0037] The piston head 10 is provided with an annular inner yoke 8, and the inner yoke 8 is provided with a Halburch permanent magnet array 7 on the outer surface of the inner y...
PUM
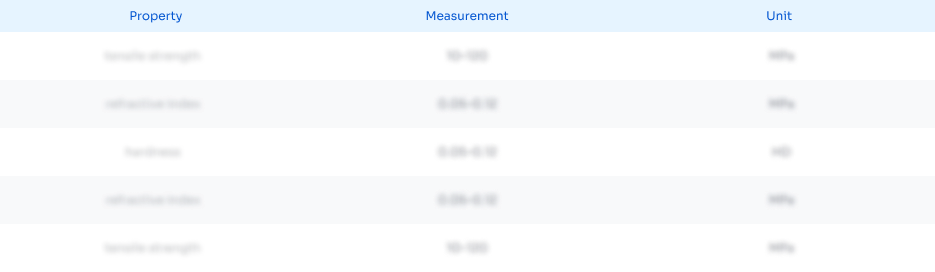
Abstract
Description
Claims
Application Information

- Generate Ideas
- Intellectual Property
- Life Sciences
- Materials
- Tech Scout
- Unparalleled Data Quality
- Higher Quality Content
- 60% Fewer Hallucinations
Browse by: Latest US Patents, China's latest patents, Technical Efficacy Thesaurus, Application Domain, Technology Topic, Popular Technical Reports.
© 2025 PatSnap. All rights reserved.Legal|Privacy policy|Modern Slavery Act Transparency Statement|Sitemap|About US| Contact US: help@patsnap.com