Non-explosive mining method utilizing 3D printing net-shaped component and barren rock for filling
A technology of 3D printing and mining methods, which is applied in ground mining, mining equipment, underground mining, etc., can solve the problems of upper and lower surrounding rock collapse, high ore dilution rate, and high mining cost, so as to reduce lifting costs and increase efficiency , Reduce the effect of surrounding rock disturbance
- Summary
- Abstract
- Description
- Claims
- Application Information
AI Technical Summary
Problems solved by technology
Method used
Image
Examples
Embodiment 1
[0040] Such as Figure 1~Figure 6 , Figure 9 and Figure 10 As shown, this embodiment provides a non-explosive mining method for filling with 3D printed mesh components and waste rocks. The mining method includes:
[0041] S110, the construction roadway, in the upper middle section of the ore body 3, construct the upper roadway inside the ore body 3 along the direction of the ore body 3, and construct the lower roadway in the lower middle section of the ore body 3 along the horizontal direction at the footwall of the ore body 3 roadway;
[0042] S120, mining of the ore body 3, first use the low and high torque raise drilling machine 5 to drill the hole 4 in the middle of the ore body 3, and then use the cutter head of the low and high torque raise drilling machine 5 to cut the broken parts in the ore body 3 from bottom to top The ore body, the broken ore body is cut into powdery ore body 6, and the powdery ore body 6 falls into the lower roadway, and the goaf 7 is formed in ...
Embodiment 2
[0047] Such as Figure 1~Figure 6 , Figure 9 , Figure 11 and Figure 12 As shown, this embodiment provides a non-explosive mining method for filling with 3D printed mesh components and waste rocks. The mining method includes:
[0048] S210. Dividing the ore body 3, dividing the ore body 3 into mine houses 31 and ore pillars 32 along the strike of the ore body 3, and the mine houses 31 and ore pillars 32 are sequentially distributed at intervals.
[0049] S220, the construction roadway, in the upper middle section of the ore body 3, construct the upper vein transportation lane 11 inside the mine house 31 along the direction of the ore body 3, and construct the upper vein roadway 21 inside the ore body 3; in the ore body 3 In the lower middle section of the mine building 31, the lower vein roadway 12 is constructed at the bottom wall of the mine house 31 along the horizontal direction, and the lower vein tunnel 22 is constructed at the bottom wall of the ore pillar 32.
[...
Embodiment 3
[0062] Such as Figure 7 and Figure 8 As shown, this embodiment provides a non-explosive mining method using 3D printing mesh components and waste rocks for filling. On the basis of the mining method provided in Embodiment 2, the mining method implemented in this implementation is mining in ore body 3 In the process of filling the goaf 7 with waste rock 9, a mine 31 is firstly mined in the mine 31, and after the mining in the mine 31 is completed, the ore pillar goaf 72 formed in the mine 31 is filled with waste rock 9; Then the ore pillar 32 adjacent to the mine house 31 is mined. After the ore pillar 32 is mined, the ore pillar goaf 72 formed in the ore pillar 32 is filled with waste rock 9 .
PUM
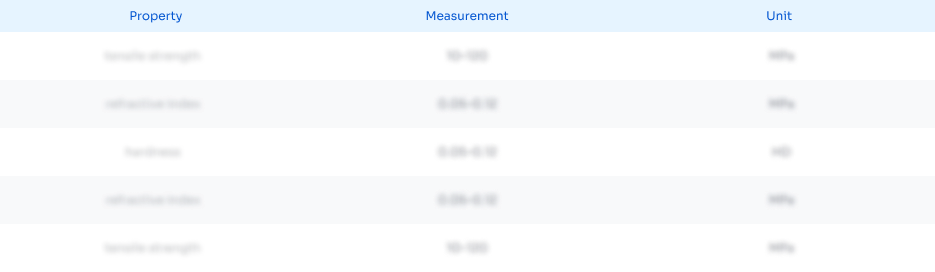
Abstract
Description
Claims
Application Information

- R&D Engineer
- R&D Manager
- IP Professional
- Industry Leading Data Capabilities
- Powerful AI technology
- Patent DNA Extraction
Browse by: Latest US Patents, China's latest patents, Technical Efficacy Thesaurus, Application Domain, Technology Topic, Popular Technical Reports.
© 2024 PatSnap. All rights reserved.Legal|Privacy policy|Modern Slavery Act Transparency Statement|Sitemap|About US| Contact US: help@patsnap.com