A driving wind tunnel test system for simulating the actual vibration form of structures
A kind of wind tunnel test, driven technology, applied in the field of wind tunnel test, can solve the problems that buildings cannot bend and vibrate, and simulation devices and systems have not yet been seen, and achieve the effect of making up for repeated use, saving test time, and improving simulation accuracy.
- Summary
- Abstract
- Description
- Claims
- Application Information
AI Technical Summary
Problems solved by technology
Method used
Image
Examples
Embodiment Construction
[0040] The present invention will be further described below in conjunction with the accompanying drawings and specific embodiments, so that those skilled in the art can better understand the present invention, the embodiments given are not used as a qualification of the present invention.
[0041] as Figure 1 As shown, the present invention comprises a numerical control circuit assembly, a driving vibration component and a multi-degree of freedom structure assembly three major parts. The numerical control circuit components are the input terminal and the emitter terminal, which mainly controls the movement of the driving vibration component under certain set test conditions; The drive-type vibration component can complete the synchronous asynchronous movement of the horizontal X, Y and Z torsional directions driven by the motor by relying on the mechanical structure shown in it, and the amplitude, frequency, phase, switch, etc. of all parties upwards are all CNC adjustable; The m...
PUM
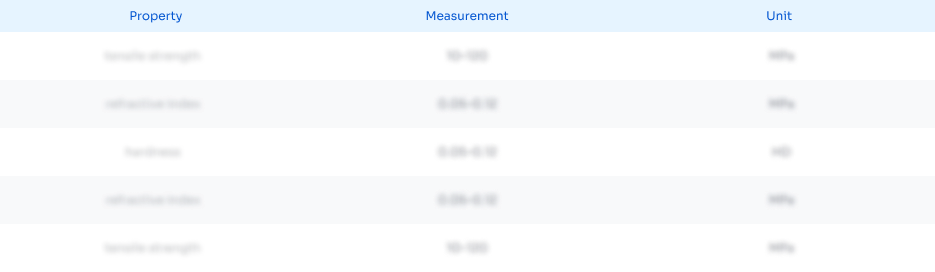
Abstract
Description
Claims
Application Information

- Generate Ideas
- Intellectual Property
- Life Sciences
- Materials
- Tech Scout
- Unparalleled Data Quality
- Higher Quality Content
- 60% Fewer Hallucinations
Browse by: Latest US Patents, China's latest patents, Technical Efficacy Thesaurus, Application Domain, Technology Topic, Popular Technical Reports.
© 2025 PatSnap. All rights reserved.Legal|Privacy policy|Modern Slavery Act Transparency Statement|Sitemap|About US| Contact US: help@patsnap.com