Connecting structure for machining driving motor shaft
A technology for connecting structures and driving motors, which is applied to metal processing machinery parts, metal processing, metal processing equipment, etc., can solve the problems of reduced motor life, low efficiency of motor shafts, and many times of motor start-up, so as to speed up mass production, The effect of speeding up efficiency
- Summary
- Abstract
- Description
- Claims
- Application Information
AI Technical Summary
Problems solved by technology
Method used
Image
Examples
Embodiment 1
[0030] see figure 1 , figure 2 , image 3 , Figure 4 , Figure 5 , Figure 6 , Figure 7 , a connection structure for processing drive motor shafts, including an outer cylinder 1, an annular groove 2 is opened on the front and back of the outer cylinder 1, an annular frame 3 is slidably connected to the inside of the annular groove 2, and a connecting frame 3 is fixedly connected to the outer side of the annular frame 3 The inner side of the connecting frame is fixedly connected with a straight rod 8, and the end of the straight rod 8 away from the connecting frame is fixedly connected with a transmission device. Adjustment device.
[0031] The connecting frame consists of a U-shaped frame 4 and a driven tooth surface rotating cylinder 25. There is an insertion hole 5 between the front and the back of the U-shaped frame 4, and the driven tooth surface rotating cylinder 25 is movably inserted into the insertion hole 5. , the fixed connection part with the ring frame 3 ...
Embodiment 2
[0036] see figure 2 , Figure 5 , The fronts of the U-shaped frame 4 and the straight rod 8 are fixedly connected with a clamping device.
[0037] The clamping device comprises a fixed head 13, a moving head 23, a clamping connecting rod 12, a threaded rod 14 and a clamping nut 22, and the clamping connecting rod 12 and the threaded rod 14 are fixedly connected with the outer wall of the driven tooth surface drum 25, and the clamping One end of the tight connecting rod 12 away from the driven tooth surface drum 25 is fixedly connected with the fixed head 13. The threaded rod 14 runs through the moving head 23. Clamp nut 22.
[0038] By rotating the clamping nuts 22 at different positions, the multiple clamping nuts 22 are moved to different positions respectively, so as to achieve the effect of multiple paired moving heads 23 and fixed heads 13 clamping motor shafts of different specifications, thereby realizing Start the motor 11 at one time to realize the function of pro...
Embodiment 3
[0040] see figure 1 , figure 2 , Figure 5 , the tooth surface of the outer wall of the clamping nut 22 is meshed with the bottom tooth surface drum 24, the bottom tooth surface drum 24 is fixedly socketed with the active tooth surface drum 10 through the ball bearing, and the inner side of the bottom tooth surface drum 24 is The extreme position is located outside when the clamping nut 22 is at the innermost side.
[0041] By rotating the bottom tooth surface drum 24, the multiple clamping nuts 22 engaged with the bottom tooth surface of the bottom tooth surface drum 24 are driven to rotate. The threaded surface of the inner wall of the clamping nut 22 is threadedly connected with the threaded rod 14, so that the clamping nut 22 moves along the threaded rod 14 during the rotation, so that the multiple moving heads 23 can be moved in the same direction along the threaded rod 14. Adjustment, so as to realize the adjustment of the distance between the multiple moving heads 2...
PUM
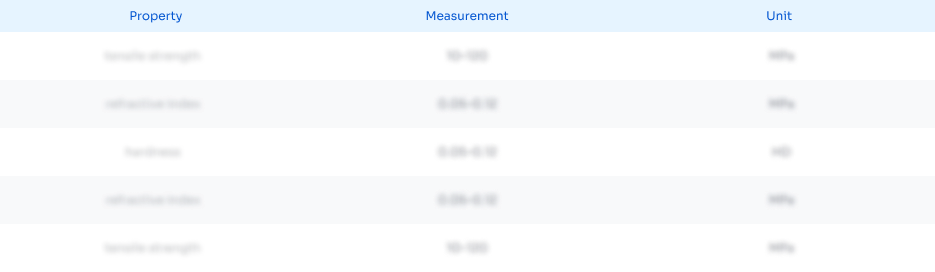
Abstract
Description
Claims
Application Information

- Generate Ideas
- Intellectual Property
- Life Sciences
- Materials
- Tech Scout
- Unparalleled Data Quality
- Higher Quality Content
- 60% Fewer Hallucinations
Browse by: Latest US Patents, China's latest patents, Technical Efficacy Thesaurus, Application Domain, Technology Topic, Popular Technical Reports.
© 2025 PatSnap. All rights reserved.Legal|Privacy policy|Modern Slavery Act Transparency Statement|Sitemap|About US| Contact US: help@patsnap.com