Method for manufacturing rock wool by using reducing agent graphene
A technology of graphene and reducing agent, applied in manufacturing tools, glass manufacturing equipment, etc., can solve the problems of huge coke waste, reduced production capacity, and elevated melting zone, so as to achieve sufficient and durable coke combustion, reduce exhaust gas emissions, and coke combustion More effect
- Summary
- Abstract
- Description
- Claims
- Application Information
AI Technical Summary
Problems solved by technology
Method used
Examples
Embodiment Construction
[0017] In order to enable those skilled in the art to better understand that the technical solutions of the present invention can be implemented, the present invention will be further described below in conjunction with specific examples, but the given examples are only used as illustrations of the present invention, not as limitations of the present invention.
[0018] A method for producing rock wool by using the reducing agent graphene, mainly using basalt cuttings as a raw material, natural gas as a fuel, and graphene as a reducing agent. The method for producing rock wool includes the following process flow:
[0019] S1. Transport the raw materials to the raw material warehouse by car, add graphene according to a certain ratio, automatically weigh and send to the batching hopper, and melt into the natural gas furnace through the batching hopper elevator according to the instructions issued by the melting material level, and the raw materials are melted in the furnace , the...
PUM
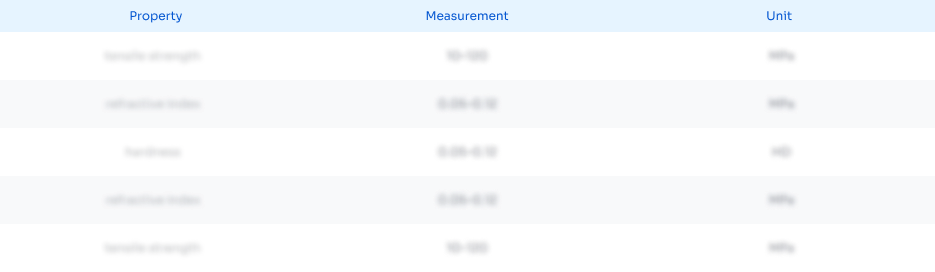
Abstract
Description
Claims
Application Information

- R&D Engineer
- R&D Manager
- IP Professional
- Industry Leading Data Capabilities
- Powerful AI technology
- Patent DNA Extraction
Browse by: Latest US Patents, China's latest patents, Technical Efficacy Thesaurus, Application Domain, Technology Topic, Popular Technical Reports.
© 2024 PatSnap. All rights reserved.Legal|Privacy policy|Modern Slavery Act Transparency Statement|Sitemap|About US| Contact US: help@patsnap.com