Production method of drum paper carcass
A production method and carcass technology, which is applied in the field of drum paper carcass production, can solve the problems of increasing raw material costs, difficulty in meeting user requirements, and high cost
- Summary
- Abstract
- Description
- Claims
- Application Information
AI Technical Summary
Problems solved by technology
Method used
Examples
Embodiment 1
[0032] The drum paper carcass production method described in the embodiment of the present invention comprises the following steps:
[0033] S1, mixing the fiber material and water, and breaking the fiber material to form a fiber slurry;
[0034] S2. Quantitatively taking out the fiber slurry and molding it to form an initial pressed piece;
[0035] S3, immersing the initial pressing piece in the colorant liquid for a second preset time to form an initial pressing piece with colorant;
[0036] S4, extracting the moisture of the initial pressing part with coloring material to form a semi-finished product;
[0037] S5. Hot pressing the semi-finished product to form a primary product.
[0038] In one embodiment, step S1 specifically includes: mixing the fiber material and water according to a preset ratio, soaking the fiber material for a first preset time, and crushing the fiber material to form a fiber slurry. After soaking for a period of time and then smashing, the fiber m...
Embodiment 2
[0059] The embodiment of the present invention differs from the first embodiment in that it further includes the following step S6: dispersing the impregnating liquid onto the primary product to form a pre-product; removing moisture from the pre-product, heating and curing to obtain a finished product. The primary product is immersed in the immersion liquid and then solidified. The colloid in the immersion liquid adheres to the surface of the primary product, which can not only play a waterproof role, but also encapsulate the coloring material to ensure that the finished product will not fade.
[0060] In one embodiment, step S6 is specifically: placing the preliminary product on the mold, dispersing the immersion liquid from above the preliminary product onto the preliminary product, maintaining the third preset time to form the pre-finished product, and removing the moisture of the pre-finished product, Heating and curing to obtain finished products. Among them, the bottom o...
PUM
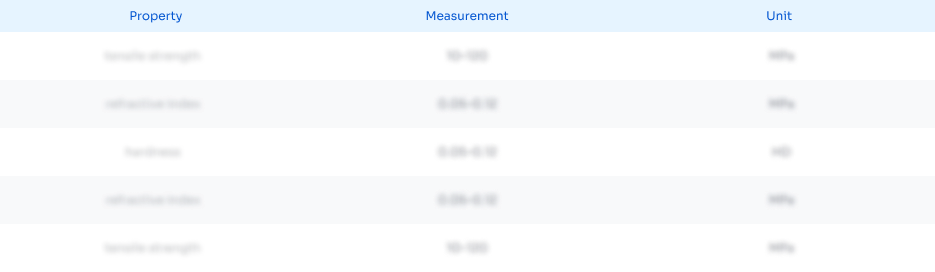
Abstract
Description
Claims
Application Information

- R&D
- Intellectual Property
- Life Sciences
- Materials
- Tech Scout
- Unparalleled Data Quality
- Higher Quality Content
- 60% Fewer Hallucinations
Browse by: Latest US Patents, China's latest patents, Technical Efficacy Thesaurus, Application Domain, Technology Topic, Popular Technical Reports.
© 2025 PatSnap. All rights reserved.Legal|Privacy policy|Modern Slavery Act Transparency Statement|Sitemap|About US| Contact US: help@patsnap.com