Variable-damping flexibly-driven exoskeleton joint
An exoskeleton and variable damping technology, which is applied in the direction of manufacturing tools, program-controlled manipulators, manipulators, etc., can solve the problems of limiting the wearer's flexibility and comfort, high energy consumption, and high rigidity of exoskeleton joints, so as to expand effective contact The effect of area, fast generation and interruption speed, and improvement of wearing comfort
- Summary
- Abstract
- Description
- Claims
- Application Information
AI Technical Summary
Problems solved by technology
Method used
Image
Examples
Embodiment Construction
[0035] The present invention will be described in further detail below in conjunction with the accompanying drawings.
[0036] Such as figure 1 Shown: The patent of this invention is designed for the exoskeleton joints driven by variable damping and compliance, which is the most important part of the exoskeleton. The overall structure of variable damping compliant drive joint unit is as follows: figure 1 shown. It mainly includes three parts: a crank slider series elastic driver 1, an exoskeleton joint shell 2 and a magneto-rheological damper 3. exist figure 2 In the explosion diagram of the overall structure of the variable damping compliant drive joint, we can see the relationship between the various parts: the entire joint unit is based on the outer skeleton joint shell 2, with copper pillars 4, shell support plate 1-5, and shell support plate 26. Shell support plate 37 connects the upper and lower exoskeleton joint shells 2, and puts two joint rolling bearings 8 into ...
PUM
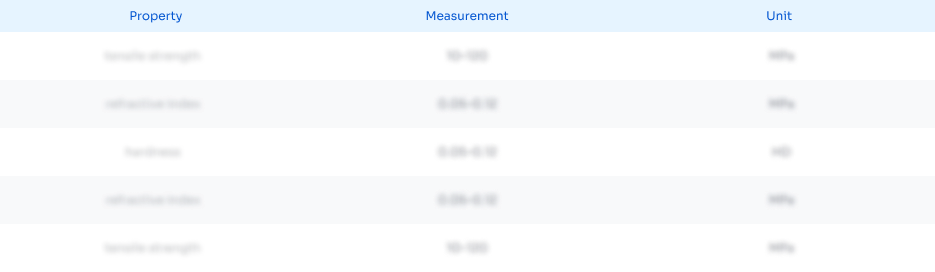
Abstract
Description
Claims
Application Information

- R&D
- Intellectual Property
- Life Sciences
- Materials
- Tech Scout
- Unparalleled Data Quality
- Higher Quality Content
- 60% Fewer Hallucinations
Browse by: Latest US Patents, China's latest patents, Technical Efficacy Thesaurus, Application Domain, Technology Topic, Popular Technical Reports.
© 2025 PatSnap. All rights reserved.Legal|Privacy policy|Modern Slavery Act Transparency Statement|Sitemap|About US| Contact US: help@patsnap.com